应用案例
您当前的位置:产品应用
一种轴瓦自动焊接装置及方法
一种轴瓦自动焊接装置及方法
【申请公布号:CN109759763A;申请权利人:张家港江苏科技大学产业技术研究院;发明设计人:张德义; 高进可; 穆开洪; 万嵘; 方海峰; 周健; 王琪;】
摘要:
本发明提供了一种轴瓦自动焊接装发置及方法,当轴瓦尺寸规格不同时,可以自动选择合适的夹持方法;焊接模块有两个同步带导轨,焊枪和送丝机固定在一个同步带导轨两端,用同步带导轨来调节焊接加工的位置,焊接完成后另一根同步带导轨上的毛刷会对焊接位置进行刷洗,一对导轨槽模块和焊接模块通过多个滑块固定在支撑模块上,通过电机驱动来调节导轨槽模块和焊接模块在支撑模块上的位置,以适合轴瓦的安放;卡盘夹紧模块采用液压三爪卡盘,采用两台螺旋升降机来调节液压三爪卡盘的工作位置,轴瓦一侧用三爪卡盘固定。
主权项:
1.一种轴瓦自动焊接装置,用于对一滑动轴承的轴瓦进行自动焊接,其特征在于,包括支撑模块及设置于所述支撑模块上的导轨槽模块、卡盘夹紧模块和焊接模块,所述轴瓦置于所述导轨槽模块上;所述导轨槽模块包括两个轴瓦支座单元,所述轴瓦支座单元包括第一电机、导轨槽、主动摩擦轮和从动摩擦轮,所述导轨槽内设置有两个第一导轨,所述主动摩擦轮和所述从动摩擦轮的两端分别设置于两个所述第一导轨上,所述第一电机驱动所述主动摩擦轮;所述焊接模块包括一竖直的焊接支架、第二电机及两个同步带导轨,所述焊接支架上设置有一第一丝杠,两个所述同步带导轨均水平安装在第一丝杠上,一个所述同步带导轨靠近轴瓦的一端设置有焊枪、另一端上设置有送丝机,另一个所述同步带导轨靠近轴瓦的一端上设置有毛刷,所述第二电机驱动所述第一丝杠转动,以调节两个所述同步带导轨在竖直方向上的位置;所述卡盘夹紧模块包括螺旋升降机及液压三爪卡盘,所述螺旋升降机用于驱动所述液压三爪卡盘沿竖直方向运动,以调整液压三爪卡盘的高度。
要求:
1.一种轴瓦自动焊接装置,用于对一滑动轴承的轴瓦进行自动焊接,其特征在于,包括支撑模块及设置于所述支撑模块上的导轨槽模块、卡盘夹紧模块和焊接模块,所述轴瓦置于所述导轨槽模块上;
所述导轨槽模块包括两个轴瓦支座单元,所述轴瓦支座单元包括第一电机、导轨槽、主动摩擦轮和从动摩擦轮,所述导轨槽内设置有两个第一导轨,所述主动摩擦轮和所述从动摩擦轮的两端分别设置于两个所述第一导轨上,所述第一电机驱动所述主动摩擦轮;
所述焊接模块包括一竖直的焊接支架、第二电机及两个同步带导轨,所述焊接支架上设置有一第一丝杠,两个所述同步带导轨均水平安装在第一丝杠上,一个所述同步带导轨靠近轴瓦的一端设置有焊枪、另一端上设置有送丝机,另一个所述同步带导轨靠近轴瓦的一端上设置有毛刷,所述第二电机驱动所述第一丝杠转动,以调节两个所述同步带导轨在竖直方向上的位置;
所述卡盘夹紧模块包括螺旋升降机及液压三爪卡盘,所述螺旋升降机用于驱动所述液压三爪卡盘沿竖直方向运动,以调整液压三爪卡盘的高度。
2.如权利要求1所述的轴瓦自动焊接装置,其特征在于,所述支撑模块的表面设置有两个第二导轨及位于两个所述第二导轨之间的第二丝杠和第一双向丝杠,两个所述导轨槽的均底部与第一双向丝杠第二丝杠连接,且两个所述导轨槽分别位于第一双向丝杠的左螺旋段和右螺旋段上,所述焊接支架的底部与所述第二丝杠连接,两个所述导轨槽的两端及所述焊接支架的两端分别设置于两个所述第二导轨上,所述第二丝杠和第一双向丝杠上各连接有一个第三电机。
3.如权利要求2所述的轴瓦自动焊接装置,其特征在于,所述导轨槽的两个所述第一导轨之间还设置有第二双向丝杠,所述主动摩擦轮和所述从动摩擦轮均与所述第二双向丝杠螺纹连接,且所述主动摩擦轮和所述从动摩擦轮分别位于第二双向丝杠的左螺旋段和右螺旋段上,每个所述轴瓦支座单元还包括一第四电机,所述第四电机通过驱动所述第二双向丝杠旋转以调节所述主动摩擦轮和所述从动摩擦轮之间的距离。
4.如权利要求1所述的轴瓦自动焊接装置,其特征在于,所述液压三爪卡盘的卡爪部分呈阶梯型。
5.如权利要求1所述的轴瓦自动焊接装置,其特征在于,所述毛刷上安装有粗糙度仪传感器。
6.一种利用如权利要求1-5中任一项所述的轴瓦自动焊接装置进行轴瓦自动焊接的方法,其特征在于,包括:
步骤S1:当轴瓦的直径尺寸d范围为200mm≤d≤400mm时,根据轴瓦的尺寸调整主动摩擦轮和从动摩擦轮之间的间距、两个轴瓦支座单元之间的间距,并将轴瓦放置在两个轴瓦支座单元上;
步骤S2:启动第一电机,以驱动所述轴瓦旋转;
步骤S3:焊枪对所述轴瓦的内表面进行焊接,焊接后粗糙度仪传感器对轴瓦内壁焊接位置进行粗糙度检测,若检测不合格,焊枪自动补焊,直至检测合格为止;
步骤S4:毛刷对焊接部位进行刷洗;
重复执行步骤S3和步骤S4,直至所述轴瓦焊接完毕。
7.一种利用如权利要求1-5中任一项所述的轴瓦自动焊接装置进行轴瓦自动焊接的方法,其特征在于,包括:
步骤S1’:当轴瓦的直径尺寸d大于400mm时,启动螺旋升降机,根据所述轴瓦的尺寸调整液压三爪卡盘的工作位置;
步骤S2’:用液压三爪卡盘夹紧轴瓦内壁,并带动所述轴瓦旋转;
步骤S3’:焊枪对所述轴瓦的内表面进行焊接,焊接后粗糙度仪传感器对轴瓦内壁焊接位置进行粗糙度检测,若检测不合格,焊枪自动补焊,直至检测合格为止;
步骤S4’:毛刷对焊接部位进行刷洗;
重复执行步骤S3’和步骤S4’,直至所述轴瓦焊接完毕。
一种轴瓦自动焊接装置及方法
技术领域
本发明涉及轴瓦加工生产设备领域,尤其涉及一种轴瓦自动焊接装发置方法。
背景技术
滑动轴承是大型机械里的重要零件,轴瓦在滑动轴承安装中是和轴颈直接接触的部分,由于轴瓦工作环境的需要,故要求轴瓦工作表面的摩擦系数要小、和足够的疲劳强度、较好的跑合能力以及良好的耐腐蚀性。为了使轴承有效工作,轴瓦内表面合金层的添加尤为必要。
在工艺上传统的方法采用的是浇注或压合的方法,传统的加工工艺方法不仅会使金属自身的内部结构被破坏,导致的性能降低,容易产生偏析、脱壳、龟裂、气泡等缺陷。同时传统放大加工在轴瓦表面的材料寿命普遍较短。焊接是利用高温让基体与焊丝结合的加工方式。由于焊接温度较高,所以能使原子间实现永久连接,是属于化学冶金结合。覆盖在基体表面上的焊接层一般会认为均匀致密无孔隙的,所以焊层能承受较大的冲击和轴瓦工作时的高负载[6]。而自动化技术的发展使焊接自动化能很好的融入工业生产线,不仅适合批量生产,更能规模化生产,随着现代工业的兴起,大型机械对轴瓦的需求量越来越大,因而急需研制一种方便、实用、效率高的用于大尺寸滑动轴承轴瓦焊接的自动焊接装置。
发明内容
本发明的目的在于提供一种轴瓦自动焊接装置及方法,以适用于大尺寸滑动轴承轴瓦焊接。
为了达到上述目的,本发明提供了一种轴瓦自动焊接装置,用于对一滑动轴承的轴瓦进行自动焊接,其特征在于,包括支撑模块及设置于所述支撑模块上的导轨槽模块、卡盘夹紧模块和焊接模块,所述轴瓦置于所述导轨槽模块上;
所述导轨槽模块包括两个轴瓦支座单元,所述轴瓦支座单元包括第一电机、导轨槽、主动摩擦轮和从动摩擦轮,所述导轨槽内设置有两个第一导轨,所述主动摩擦轮和所述从动摩擦轮的两端分别设置于两个所述第一导轨上,所述第一电机驱动所述主动摩擦轮;
所述焊接模块包括一竖直的焊接支架、第二电机及两个同步带导轨,所述焊接支架上设置有一第一丝杠,两个所述同步带导轨均水平安装在第一丝杠上,一个所述同步带导轨靠近轴瓦的一端设置有焊枪、另一端上设置有送丝机,另一个所述同步带导轨靠近轴瓦的一端上设置有毛刷,所述第二电机驱动所述第一丝杠转动,以调节两个所述同步带导轨在竖直方向上的位置;
所述卡盘夹紧模块包括螺旋升降机及液压三爪卡盘,所述螺旋升降机用于驱动所述液压三爪卡盘沿竖直方向运动,以调整液压三爪卡盘的高度。
可选的,所述支撑模块的表面设置有两个第二导轨及位于两个所述第二导轨之间的第二丝杠和第一双向丝杠,两个所述导轨槽的均底部与第一双向丝杠第二丝杠连接,且两个所述导轨槽分别位于第一双向丝杠的左螺旋段和右螺旋段上,所述焊接支架的底部与所述第二丝杠连接,两个所述导轨槽的两端及所述焊接支架的两端分别设置于两个所述第二导轨上,所述第二丝杠和第一双向丝杠上各连接有一个第三电机。
可选的,所述导轨槽的两个所述第一导轨之间还设置有第二双向丝杠,所述主动摩擦轮和所述从动摩擦轮均与所述第二双向丝杠螺纹连接,且所述主动摩擦轮和所述从动摩擦轮分别位于第二双向丝杠的左螺旋段和右螺旋段上,每个所述轴瓦支座单元还包括一第四电机,所述第四电机通过驱动所述第二双向丝杠旋转以调节所述主动摩擦轮和所述从动摩擦轮之间的距离。
可选的,所述液压三爪卡盘的卡爪部分呈阶梯型。
可选的,所述毛刷上安装有粗糙度仪传感器。
根据轴瓦的直径尺寸范围,本发明还提供了两种利用所述的轴瓦自动焊接装置进行轴瓦自动焊接的方法,第一种自动焊接的方法包括:
步骤S1:当轴瓦的直径尺寸d范围为200mm≤d≤400mm时,根据轴瓦的尺寸调整主动摩擦轮和从动摩擦轮之间的间距、两个轴瓦支座单元之间的间距,并将轴瓦放置在两个轴瓦支座单元上;
步骤S2:启动第一电机,以驱动所述轴瓦旋转;
步骤S3:焊枪对所述轴瓦的内表面进行焊接,焊接后粗糙度仪传感器对轴瓦内壁焊接位置进行粗糙度检测,若检测不合格,焊枪自动补焊,直至检测合格为止;
步骤S4:毛刷对焊接部位进行刷洗;
重复执行步骤S3和步骤S4,直至所述轴瓦焊接完毕。
第二种自动焊接的方法包括:
步骤S1’:当轴瓦的直径尺寸d大于400mm时,启动螺旋升降机,根据所述轴瓦的尺寸调整液压三爪卡盘的工作位置;
步骤S2’:用液压三爪卡盘夹紧轴瓦内壁,并带动所述轴瓦旋转;
步骤S3’:焊枪对所述轴瓦的内表面进行焊接,焊接后粗糙度仪传感器对轴瓦内壁焊接位置进行粗糙度检测,若检测不合格,焊枪自动补焊,直至检测合格为止;
步骤S4’:毛刷对焊接部位进行刷洗;
重复执行步骤S3’和步骤S4’,直至所述轴瓦焊接完毕。
本发明提供的轴瓦自动焊接装置具有如下有益效果:
(1)当轴瓦尺寸规格不同时,可以自动选择合适的夹持尺寸和夹持力度;轴瓦的高度可以根据需要的加工高度进行调节,具有良好的人机工程学,在焊接自动化过程以传感器为辅,使轴瓦质量、性能大大提高,有利于轴瓦的大规模、批量化生产,以满足需求;
(2)焊接模块有两个同步带导轨,焊枪和送丝机固定在一个同步带导轨两端,用同步带导轨来调节焊接加工的位置,焊接完成后另一根同步带导轨上的毛刷会对焊接位置进行刷洗,竖直的支架一侧有一根竖直放置的丝杠,丝杠由顶端的电机带动,以实现同步带导轨位置的上下调;
(3)一对导轨槽模块和焊接模块通过多个滑块固定在支撑模块上,通过电机驱动来调节导轨槽模块和焊接模块在支撑模块上的位置,以便于轴瓦的安放;
(4)卡盘夹紧模块采用新型液压三爪卡盘,采用两台螺旋升降机来调节液压三爪卡盘的工作位置,整个机架部分的框架用选定尺寸的方钢管焊接成设计所需的形状,焊接钢管的最大高度由所需要的螺旋升降机的工作行程调定,在关键承重的地方,采用焊接加强筋进而加固,整体的框架用螺栓通过底部钢管的螺栓孔定位固定,卡爪部分呈阶梯性,分段加工,有利于轴瓦的夹持,并在卡爪内表面压合一种高强度合金,有效防止磨损,提高效率;
(5)为调节主动摩擦轮和从动摩擦轮的间距,采用水平位置调节螺杆的滑动螺旋传动,滑动螺旋还具有能够自锁的这一优点。
附图说明
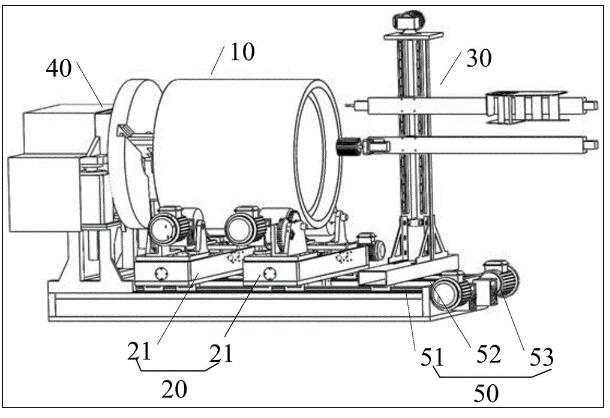
图1为本发明实施例提供的轴瓦自动焊接装置的结构示意图;
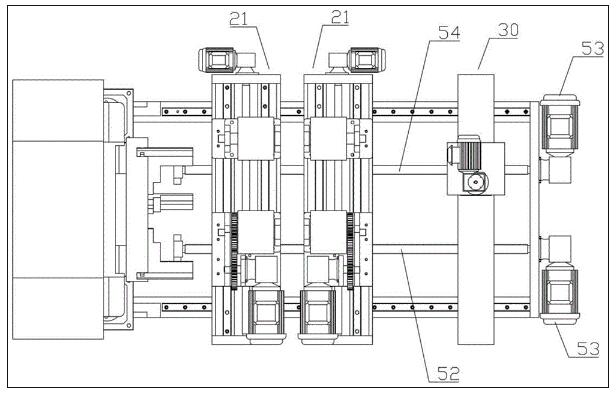
图2为本发明实施例提供的轴瓦自动焊接装置的俯视图;
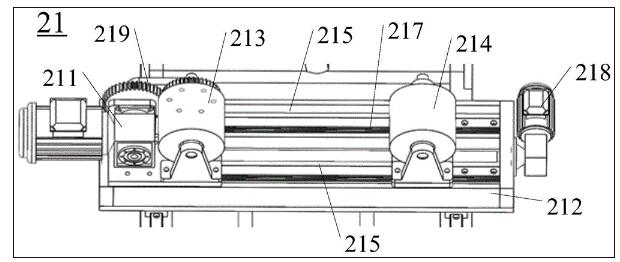
图3为本发明实施例提供的轴瓦自动焊接装置的导轨槽模块的结构示意图;
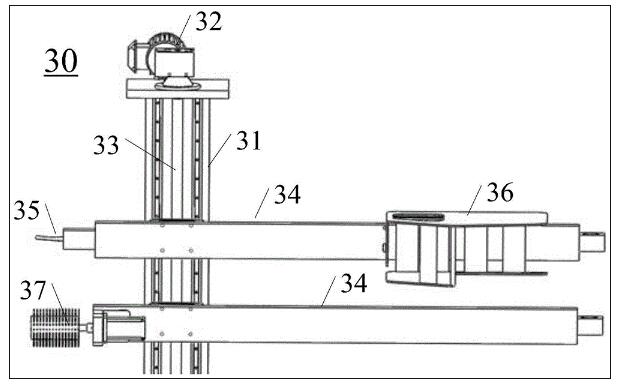
图4为本发明实施例提供的轴瓦自动焊接装置的焊接模块的结构示意图;
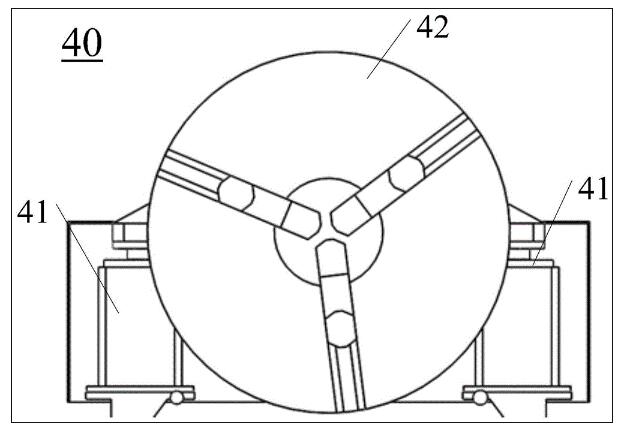
图5为本发明实施例提供的轴瓦自动焊接装置的卡盘夹紧模块的结构示意图;
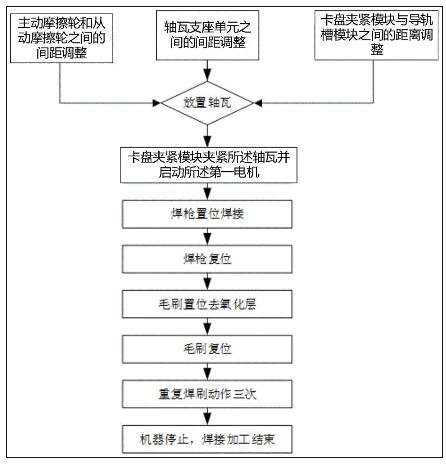
图6为本发明实施例提供的轴瓦自动焊接方法的流程图;
其中,附图标记为:
10-轴瓦;20-导轨槽模块;21-轴瓦支座单元;211-第一电机;212-导轨槽;213-主动摩擦轮;214-从动摩擦轮;215-第一导轨;217-第二双向丝杠;218-第四电机;219-主动齿轮;30-焊接模块;31-焊接支架;32-第二电机;33-第一丝杠;34-同步带导轨;35-焊枪;36-送丝机;37-毛刷;40-卡盘夹紧模块;41-螺旋升降机;42-液压三爪卡盘;50-支撑模块;51-第二导轨;52-第二丝杠;53-第三电机;54-第一双向丝杠。
具体实施方式
下面将结合示意图对本发明的具体实施方式进行更详细的描述。根据下列描述和权利要求书,本发明的优点和特征将更清楚。需说明的是,附图均采用非常简化的形式且均使用非精准的比例,仅用以方便、明晰地辅助说明本发明实施例的目的。
请参阅如1-图5,本实施例提供了一种轴瓦10自动焊接装置,用于对一滑动轴承的轴瓦10进行自动焊接,包括支撑模块50及设置于所述支撑模块50上的导轨槽模块20、卡盘夹紧模块40和焊接模块30,所述轴瓦10置于所述导轨槽模块20上,所述卡盘夹紧模块40用于夹持所述轴瓦10的端部,所述焊接模块30用于对所述轴瓦10的内壁进行焊接加工。
具体的,如图3所示,所述导轨槽模块20具有两个轴瓦支座单元21,用于承载所述轴瓦10的侧壁,即所述轴瓦10横向设置于所述两个所述轴瓦支座单元21上,所述轴瓦支座单元21包括第一电机211、导轨槽212、主动摩擦轮213和从动摩擦轮214,所述从动摩擦轮214内有一对深沟球轴承,通过从动轴转动安装在一支座上,所述主动摩擦轮213与从动摩擦轮214相似,不同之处在于主动摩擦轮213上啮合了主动齿轮219,主动齿轮219安装在第一电机211的转轴上,第一电机211通过主动齿轮219驱动主动摩擦轮213转动,主动摩擦轮213转动通过摩擦力来带动轴瓦10的转动。
进一步,所述导轨槽212内设置有第二双向丝杠217及平行设置于所述第二双向丝杠217两侧的两个第一导轨215,所述主动摩擦轮213和从动摩擦轮214的两端设置于两个所述第一导轨215上便于滑动,所述第二双向丝杠217为双向丝杠,所述主动摩擦轮213和所述从动摩擦轮214的支座均与所述第二双向丝杠217螺纹连接,所述主动摩擦轮213和所述从动摩擦轮214分别位于第二双向丝杠217的左螺旋段和右螺旋段上,第四电机218驱动所述第二双向丝杠217转动以改变所述主动摩擦轮213和所述从动摩擦轮214之间的距离,以便于不同尺寸轴瓦10的安放。
如图4所示,所述焊接模块30具有一矩形钢底座,所述矩形钢底座上设置有一竖直的焊接支架31,所述焊接支架31通过三角固定架固定在所述矩形钢底座上,所述焊接支架31的一侧安装有两个同步带导轨34,上层同步带导轨34的前端固定有一把焊枪35,而其后端则固定输送焊丝的送丝机34。下层同步带导轨34前端固定有毛刷37,焊接支架31一侧设置有一第一丝杠33,所述焊接支架31顶部设置有第二电机32,以带动第一丝杠33的旋转,两个同步带导轨均安装在第一丝杠33上,通过第一丝杠33转动调节两个所述同步带导轨34在竖直方向上的位置,达到调整焊枪35和毛刷37工作位置的目的。每个所述同步带导轨34均具有自配的伺服电机来实现其前伸和后缩的动作。焊接完成后,毛刷37会对焊接位置刷洗,并且所述毛刷37表面装有粗糙度仪传感器,对轴瓦10内表面进行粗糙度检测,若检测合格,停止焊接、刷洗,进行下一步操作;若检测不合格,焊枪35自动补焊,再刷洗。
进一步,如图5所示,所述卡盘夹紧模块40包括螺旋升降机41及液压三爪卡盘42,所述螺旋升降机41具有两个,两个所述螺旋升降机41用于驱动所述液压三爪卡盘42沿竖直方向运动,以调节所述液压三爪卡盘42的工作位置,整个所述卡盘夹紧模块40机架部分的框架用选定尺寸的方钢管焊接成设计所需的形状,焊接钢管的最大高度由所需要的螺旋升降机41的工作行程调定,在关键承重的地方,焊接加强筋进而加固,整体的框架用螺栓通过底部钢管的螺栓孔定位固定。
可选的,所述液压三爪卡盘42的卡爪部分呈阶梯型,分段加工,有利于轴瓦10的夹持,有利于轴瓦10的夹持,在卡爪内表面压合一种高强度合金层,有效防止磨损,提高效率。
进一步,所述卡爪与所述轴瓦10接触的部分上可以设置一压力传感器,用于探测所述液压三爪卡的夹持力,一方面可以防止夹持力不足,导致轴瓦10脱落,一方面防止夹持力过大,损坏轴瓦10。
如图1和图2所示,所述支撑模块50为整个所述轴瓦10自动焊接装置提供支撑,且所述支撑模块50的表面设置有两个第二导轨51及位于两个所述第二导轨51之间的第二丝杠52和第一双向丝杠54,两个所述导轨槽212的底部与所述第一双向丝杠54螺纹连接,且两个所述导轨槽212分别位于第一双向丝杠54的左螺旋段和右螺旋段上,所述焊接支架31的底部与所述第二丝杠52螺纹连接,两个所述导轨槽212的两端及所述焊接支架31的两端分别设置于两个所述第二导轨51上,所述第二丝杠52和第一双向丝杠54上各连接有一个第三电机53,对应的所述第三电机53分别用于驱动所述第二丝杠52和第一双向丝杠54转动,以改变两个所述轴瓦支座单元21之间的间距及所述焊接模块30在所述支撑模块50上的横向位置。
基于此,如图1-6所示,本实施例根据轴瓦10的直径尺寸范围,提供了两种利用所述轴瓦10自动焊接装置进行轴瓦10自动焊接的方法,第一种方法的步骤包括:
步骤S1:当轴瓦10的直径尺寸d范围为200mm≤d≤400mm时,根据轴瓦10的尺寸调整主动摩擦轮213和从动摩擦轮214之间的间距、两个轴瓦支座单元21之间的间距,并将所述轴瓦10放置在两个轴瓦支座单元21上;
步骤S2:启动第一电机211,所述主动摩擦轮213带动所述轴瓦10旋转;
步骤S3:焊枪35对所述轴瓦10的内表面进行焊接,焊接后粗糙度仪传感器对轴瓦10内壁焊接位置进行粗糙度检测,若检测不合格,焊枪35自动补焊,直至检测合格为止;
步骤S4:毛刷37对焊接部位进行刷洗;
重复执行步骤S3和步骤S4,直至所述轴瓦10焊接完毕。
第二种方法的步骤包括:
步骤S1’:当轴瓦10的直径尺寸d大于400mm时,启动螺旋升降机41,根据所述轴瓦10的尺寸调整液压三爪卡盘42的工作位置;
步骤S2’:用液压三爪卡盘42夹紧轴瓦10内壁,并带动所述轴瓦10旋转;
步骤S3’:焊枪35对所述轴瓦10的内表面进行焊接,焊接后粗糙度仪传感器对轴瓦10内壁焊接位置进行粗糙度检测,若检测不合格,焊枪35自动补焊,直至检测合格为止;
步骤S4’:毛刷37对焊接部位进行刷洗;
重复执行步骤S3’和步骤S4’,直至所述轴瓦焊接完毕。
上述仅为本发明的优选实施例而已,并不对本发明起到任何限制作用。任何所属技术领域的技术人员,在不脱离本发明的技术方案的范围内,对本发明揭露的技术方案和技术内容做任何形式的等同替换或修改等变动,均属未脱离本发明的技术方案的内容,仍属于本发明的保护范围之内。
【申请公布号:CN109759763A;申请权利人:张家港江苏科技大学产业技术研究院;发明设计人:张德义; 高进可; 穆开洪; 万嵘; 方海峰; 周健; 王琪;】
摘要:
本发明提供了一种轴瓦自动焊接装发置及方法,当轴瓦尺寸规格不同时,可以自动选择合适的夹持方法;焊接模块有两个同步带导轨,焊枪和送丝机固定在一个同步带导轨两端,用同步带导轨来调节焊接加工的位置,焊接完成后另一根同步带导轨上的毛刷会对焊接位置进行刷洗,一对导轨槽模块和焊接模块通过多个滑块固定在支撑模块上,通过电机驱动来调节导轨槽模块和焊接模块在支撑模块上的位置,以适合轴瓦的安放;卡盘夹紧模块采用液压三爪卡盘,采用两台螺旋升降机来调节液压三爪卡盘的工作位置,轴瓦一侧用三爪卡盘固定。
主权项:
1.一种轴瓦自动焊接装置,用于对一滑动轴承的轴瓦进行自动焊接,其特征在于,包括支撑模块及设置于所述支撑模块上的导轨槽模块、卡盘夹紧模块和焊接模块,所述轴瓦置于所述导轨槽模块上;所述导轨槽模块包括两个轴瓦支座单元,所述轴瓦支座单元包括第一电机、导轨槽、主动摩擦轮和从动摩擦轮,所述导轨槽内设置有两个第一导轨,所述主动摩擦轮和所述从动摩擦轮的两端分别设置于两个所述第一导轨上,所述第一电机驱动所述主动摩擦轮;所述焊接模块包括一竖直的焊接支架、第二电机及两个同步带导轨,所述焊接支架上设置有一第一丝杠,两个所述同步带导轨均水平安装在第一丝杠上,一个所述同步带导轨靠近轴瓦的一端设置有焊枪、另一端上设置有送丝机,另一个所述同步带导轨靠近轴瓦的一端上设置有毛刷,所述第二电机驱动所述第一丝杠转动,以调节两个所述同步带导轨在竖直方向上的位置;所述卡盘夹紧模块包括螺旋升降机及液压三爪卡盘,所述螺旋升降机用于驱动所述液压三爪卡盘沿竖直方向运动,以调整液压三爪卡盘的高度。
要求:
1.一种轴瓦自动焊接装置,用于对一滑动轴承的轴瓦进行自动焊接,其特征在于,包括支撑模块及设置于所述支撑模块上的导轨槽模块、卡盘夹紧模块和焊接模块,所述轴瓦置于所述导轨槽模块上;
所述导轨槽模块包括两个轴瓦支座单元,所述轴瓦支座单元包括第一电机、导轨槽、主动摩擦轮和从动摩擦轮,所述导轨槽内设置有两个第一导轨,所述主动摩擦轮和所述从动摩擦轮的两端分别设置于两个所述第一导轨上,所述第一电机驱动所述主动摩擦轮;
所述焊接模块包括一竖直的焊接支架、第二电机及两个同步带导轨,所述焊接支架上设置有一第一丝杠,两个所述同步带导轨均水平安装在第一丝杠上,一个所述同步带导轨靠近轴瓦的一端设置有焊枪、另一端上设置有送丝机,另一个所述同步带导轨靠近轴瓦的一端上设置有毛刷,所述第二电机驱动所述第一丝杠转动,以调节两个所述同步带导轨在竖直方向上的位置;
所述卡盘夹紧模块包括螺旋升降机及液压三爪卡盘,所述螺旋升降机用于驱动所述液压三爪卡盘沿竖直方向运动,以调整液压三爪卡盘的高度。
2.如权利要求1所述的轴瓦自动焊接装置,其特征在于,所述支撑模块的表面设置有两个第二导轨及位于两个所述第二导轨之间的第二丝杠和第一双向丝杠,两个所述导轨槽的均底部与第一双向丝杠第二丝杠连接,且两个所述导轨槽分别位于第一双向丝杠的左螺旋段和右螺旋段上,所述焊接支架的底部与所述第二丝杠连接,两个所述导轨槽的两端及所述焊接支架的两端分别设置于两个所述第二导轨上,所述第二丝杠和第一双向丝杠上各连接有一个第三电机。
3.如权利要求2所述的轴瓦自动焊接装置,其特征在于,所述导轨槽的两个所述第一导轨之间还设置有第二双向丝杠,所述主动摩擦轮和所述从动摩擦轮均与所述第二双向丝杠螺纹连接,且所述主动摩擦轮和所述从动摩擦轮分别位于第二双向丝杠的左螺旋段和右螺旋段上,每个所述轴瓦支座单元还包括一第四电机,所述第四电机通过驱动所述第二双向丝杠旋转以调节所述主动摩擦轮和所述从动摩擦轮之间的距离。
4.如权利要求1所述的轴瓦自动焊接装置,其特征在于,所述液压三爪卡盘的卡爪部分呈阶梯型。
5.如权利要求1所述的轴瓦自动焊接装置,其特征在于,所述毛刷上安装有粗糙度仪传感器。
6.一种利用如权利要求1-5中任一项所述的轴瓦自动焊接装置进行轴瓦自动焊接的方法,其特征在于,包括:
步骤S1:当轴瓦的直径尺寸d范围为200mm≤d≤400mm时,根据轴瓦的尺寸调整主动摩擦轮和从动摩擦轮之间的间距、两个轴瓦支座单元之间的间距,并将轴瓦放置在两个轴瓦支座单元上;
步骤S2:启动第一电机,以驱动所述轴瓦旋转;
步骤S3:焊枪对所述轴瓦的内表面进行焊接,焊接后粗糙度仪传感器对轴瓦内壁焊接位置进行粗糙度检测,若检测不合格,焊枪自动补焊,直至检测合格为止;
步骤S4:毛刷对焊接部位进行刷洗;
重复执行步骤S3和步骤S4,直至所述轴瓦焊接完毕。
7.一种利用如权利要求1-5中任一项所述的轴瓦自动焊接装置进行轴瓦自动焊接的方法,其特征在于,包括:
步骤S1’:当轴瓦的直径尺寸d大于400mm时,启动螺旋升降机,根据所述轴瓦的尺寸调整液压三爪卡盘的工作位置;
步骤S2’:用液压三爪卡盘夹紧轴瓦内壁,并带动所述轴瓦旋转;
步骤S3’:焊枪对所述轴瓦的内表面进行焊接,焊接后粗糙度仪传感器对轴瓦内壁焊接位置进行粗糙度检测,若检测不合格,焊枪自动补焊,直至检测合格为止;
步骤S4’:毛刷对焊接部位进行刷洗;
重复执行步骤S3’和步骤S4’,直至所述轴瓦焊接完毕。
一种轴瓦自动焊接装置及方法
技术领域
本发明涉及轴瓦加工生产设备领域,尤其涉及一种轴瓦自动焊接装发置方法。
背景技术
滑动轴承是大型机械里的重要零件,轴瓦在滑动轴承安装中是和轴颈直接接触的部分,由于轴瓦工作环境的需要,故要求轴瓦工作表面的摩擦系数要小、和足够的疲劳强度、较好的跑合能力以及良好的耐腐蚀性。为了使轴承有效工作,轴瓦内表面合金层的添加尤为必要。
在工艺上传统的方法采用的是浇注或压合的方法,传统的加工工艺方法不仅会使金属自身的内部结构被破坏,导致的性能降低,容易产生偏析、脱壳、龟裂、气泡等缺陷。同时传统放大加工在轴瓦表面的材料寿命普遍较短。焊接是利用高温让基体与焊丝结合的加工方式。由于焊接温度较高,所以能使原子间实现永久连接,是属于化学冶金结合。覆盖在基体表面上的焊接层一般会认为均匀致密无孔隙的,所以焊层能承受较大的冲击和轴瓦工作时的高负载[6]。而自动化技术的发展使焊接自动化能很好的融入工业生产线,不仅适合批量生产,更能规模化生产,随着现代工业的兴起,大型机械对轴瓦的需求量越来越大,因而急需研制一种方便、实用、效率高的用于大尺寸滑动轴承轴瓦焊接的自动焊接装置。
发明内容
本发明的目的在于提供一种轴瓦自动焊接装置及方法,以适用于大尺寸滑动轴承轴瓦焊接。
为了达到上述目的,本发明提供了一种轴瓦自动焊接装置,用于对一滑动轴承的轴瓦进行自动焊接,其特征在于,包括支撑模块及设置于所述支撑模块上的导轨槽模块、卡盘夹紧模块和焊接模块,所述轴瓦置于所述导轨槽模块上;
所述导轨槽模块包括两个轴瓦支座单元,所述轴瓦支座单元包括第一电机、导轨槽、主动摩擦轮和从动摩擦轮,所述导轨槽内设置有两个第一导轨,所述主动摩擦轮和所述从动摩擦轮的两端分别设置于两个所述第一导轨上,所述第一电机驱动所述主动摩擦轮;
所述焊接模块包括一竖直的焊接支架、第二电机及两个同步带导轨,所述焊接支架上设置有一第一丝杠,两个所述同步带导轨均水平安装在第一丝杠上,一个所述同步带导轨靠近轴瓦的一端设置有焊枪、另一端上设置有送丝机,另一个所述同步带导轨靠近轴瓦的一端上设置有毛刷,所述第二电机驱动所述第一丝杠转动,以调节两个所述同步带导轨在竖直方向上的位置;
所述卡盘夹紧模块包括螺旋升降机及液压三爪卡盘,所述螺旋升降机用于驱动所述液压三爪卡盘沿竖直方向运动,以调整液压三爪卡盘的高度。
可选的,所述支撑模块的表面设置有两个第二导轨及位于两个所述第二导轨之间的第二丝杠和第一双向丝杠,两个所述导轨槽的均底部与第一双向丝杠第二丝杠连接,且两个所述导轨槽分别位于第一双向丝杠的左螺旋段和右螺旋段上,所述焊接支架的底部与所述第二丝杠连接,两个所述导轨槽的两端及所述焊接支架的两端分别设置于两个所述第二导轨上,所述第二丝杠和第一双向丝杠上各连接有一个第三电机。
可选的,所述导轨槽的两个所述第一导轨之间还设置有第二双向丝杠,所述主动摩擦轮和所述从动摩擦轮均与所述第二双向丝杠螺纹连接,且所述主动摩擦轮和所述从动摩擦轮分别位于第二双向丝杠的左螺旋段和右螺旋段上,每个所述轴瓦支座单元还包括一第四电机,所述第四电机通过驱动所述第二双向丝杠旋转以调节所述主动摩擦轮和所述从动摩擦轮之间的距离。
可选的,所述液压三爪卡盘的卡爪部分呈阶梯型。
可选的,所述毛刷上安装有粗糙度仪传感器。
根据轴瓦的直径尺寸范围,本发明还提供了两种利用所述的轴瓦自动焊接装置进行轴瓦自动焊接的方法,第一种自动焊接的方法包括:
步骤S1:当轴瓦的直径尺寸d范围为200mm≤d≤400mm时,根据轴瓦的尺寸调整主动摩擦轮和从动摩擦轮之间的间距、两个轴瓦支座单元之间的间距,并将轴瓦放置在两个轴瓦支座单元上;
步骤S2:启动第一电机,以驱动所述轴瓦旋转;
步骤S3:焊枪对所述轴瓦的内表面进行焊接,焊接后粗糙度仪传感器对轴瓦内壁焊接位置进行粗糙度检测,若检测不合格,焊枪自动补焊,直至检测合格为止;
步骤S4:毛刷对焊接部位进行刷洗;
重复执行步骤S3和步骤S4,直至所述轴瓦焊接完毕。
第二种自动焊接的方法包括:
步骤S1’:当轴瓦的直径尺寸d大于400mm时,启动螺旋升降机,根据所述轴瓦的尺寸调整液压三爪卡盘的工作位置;
步骤S2’:用液压三爪卡盘夹紧轴瓦内壁,并带动所述轴瓦旋转;
步骤S3’:焊枪对所述轴瓦的内表面进行焊接,焊接后粗糙度仪传感器对轴瓦内壁焊接位置进行粗糙度检测,若检测不合格,焊枪自动补焊,直至检测合格为止;
步骤S4’:毛刷对焊接部位进行刷洗;
重复执行步骤S3’和步骤S4’,直至所述轴瓦焊接完毕。
本发明提供的轴瓦自动焊接装置具有如下有益效果:
(1)当轴瓦尺寸规格不同时,可以自动选择合适的夹持尺寸和夹持力度;轴瓦的高度可以根据需要的加工高度进行调节,具有良好的人机工程学,在焊接自动化过程以传感器为辅,使轴瓦质量、性能大大提高,有利于轴瓦的大规模、批量化生产,以满足需求;
(2)焊接模块有两个同步带导轨,焊枪和送丝机固定在一个同步带导轨两端,用同步带导轨来调节焊接加工的位置,焊接完成后另一根同步带导轨上的毛刷会对焊接位置进行刷洗,竖直的支架一侧有一根竖直放置的丝杠,丝杠由顶端的电机带动,以实现同步带导轨位置的上下调;
(3)一对导轨槽模块和焊接模块通过多个滑块固定在支撑模块上,通过电机驱动来调节导轨槽模块和焊接模块在支撑模块上的位置,以便于轴瓦的安放;
(4)卡盘夹紧模块采用新型液压三爪卡盘,采用两台螺旋升降机来调节液压三爪卡盘的工作位置,整个机架部分的框架用选定尺寸的方钢管焊接成设计所需的形状,焊接钢管的最大高度由所需要的螺旋升降机的工作行程调定,在关键承重的地方,采用焊接加强筋进而加固,整体的框架用螺栓通过底部钢管的螺栓孔定位固定,卡爪部分呈阶梯性,分段加工,有利于轴瓦的夹持,并在卡爪内表面压合一种高强度合金,有效防止磨损,提高效率;
(5)为调节主动摩擦轮和从动摩擦轮的间距,采用水平位置调节螺杆的滑动螺旋传动,滑动螺旋还具有能够自锁的这一优点。
附图说明
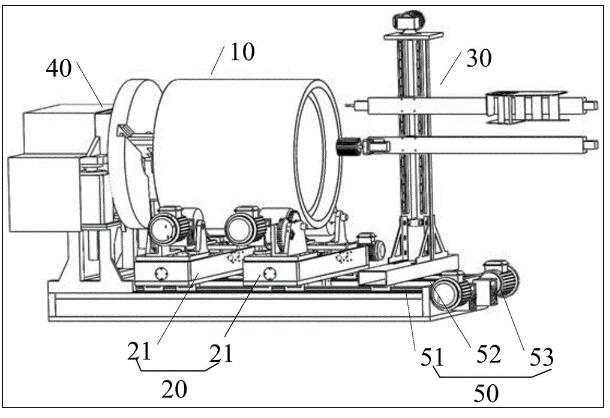
图1为本发明实施例提供的轴瓦自动焊接装置的结构示意图;
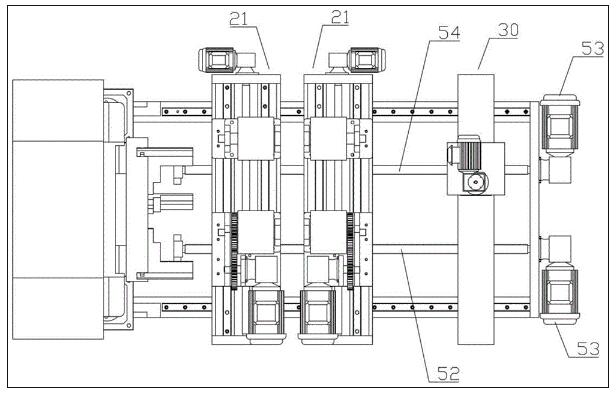
图2为本发明实施例提供的轴瓦自动焊接装置的俯视图;
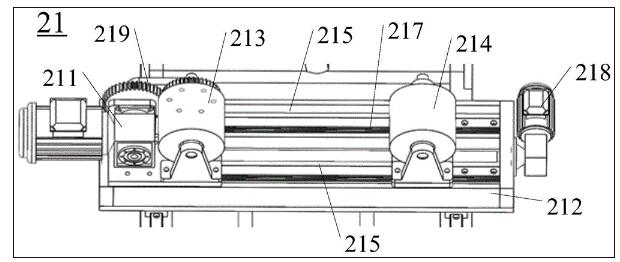
图3为本发明实施例提供的轴瓦自动焊接装置的导轨槽模块的结构示意图;
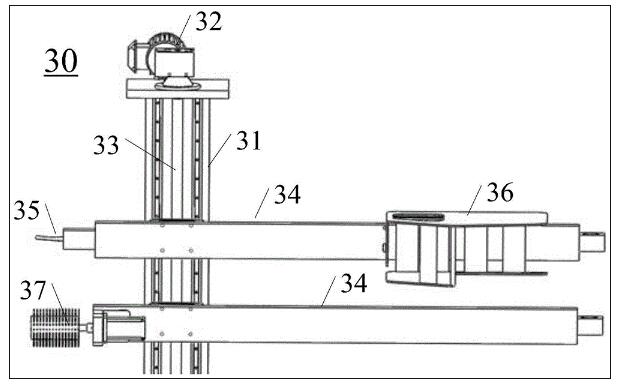
图4为本发明实施例提供的轴瓦自动焊接装置的焊接模块的结构示意图;
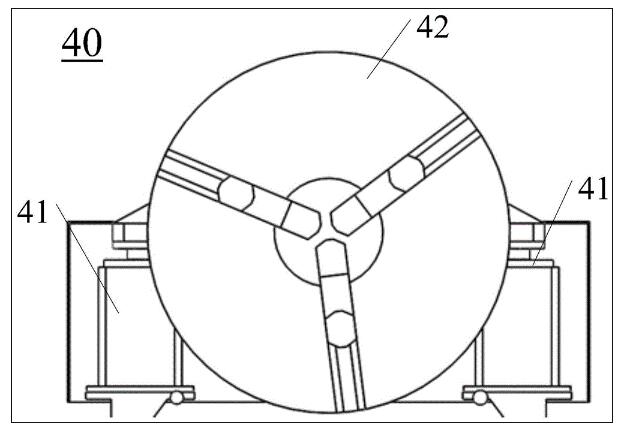
图5为本发明实施例提供的轴瓦自动焊接装置的卡盘夹紧模块的结构示意图;
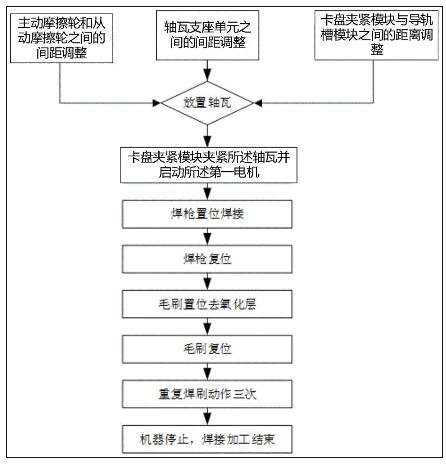
图6为本发明实施例提供的轴瓦自动焊接方法的流程图;
其中,附图标记为:
10-轴瓦;20-导轨槽模块;21-轴瓦支座单元;211-第一电机;212-导轨槽;213-主动摩擦轮;214-从动摩擦轮;215-第一导轨;217-第二双向丝杠;218-第四电机;219-主动齿轮;30-焊接模块;31-焊接支架;32-第二电机;33-第一丝杠;34-同步带导轨;35-焊枪;36-送丝机;37-毛刷;40-卡盘夹紧模块;41-螺旋升降机;42-液压三爪卡盘;50-支撑模块;51-第二导轨;52-第二丝杠;53-第三电机;54-第一双向丝杠。
具体实施方式
下面将结合示意图对本发明的具体实施方式进行更详细的描述。根据下列描述和权利要求书,本发明的优点和特征将更清楚。需说明的是,附图均采用非常简化的形式且均使用非精准的比例,仅用以方便、明晰地辅助说明本发明实施例的目的。
请参阅如1-图5,本实施例提供了一种轴瓦10自动焊接装置,用于对一滑动轴承的轴瓦10进行自动焊接,包括支撑模块50及设置于所述支撑模块50上的导轨槽模块20、卡盘夹紧模块40和焊接模块30,所述轴瓦10置于所述导轨槽模块20上,所述卡盘夹紧模块40用于夹持所述轴瓦10的端部,所述焊接模块30用于对所述轴瓦10的内壁进行焊接加工。
具体的,如图3所示,所述导轨槽模块20具有两个轴瓦支座单元21,用于承载所述轴瓦10的侧壁,即所述轴瓦10横向设置于所述两个所述轴瓦支座单元21上,所述轴瓦支座单元21包括第一电机211、导轨槽212、主动摩擦轮213和从动摩擦轮214,所述从动摩擦轮214内有一对深沟球轴承,通过从动轴转动安装在一支座上,所述主动摩擦轮213与从动摩擦轮214相似,不同之处在于主动摩擦轮213上啮合了主动齿轮219,主动齿轮219安装在第一电机211的转轴上,第一电机211通过主动齿轮219驱动主动摩擦轮213转动,主动摩擦轮213转动通过摩擦力来带动轴瓦10的转动。
进一步,所述导轨槽212内设置有第二双向丝杠217及平行设置于所述第二双向丝杠217两侧的两个第一导轨215,所述主动摩擦轮213和从动摩擦轮214的两端设置于两个所述第一导轨215上便于滑动,所述第二双向丝杠217为双向丝杠,所述主动摩擦轮213和所述从动摩擦轮214的支座均与所述第二双向丝杠217螺纹连接,所述主动摩擦轮213和所述从动摩擦轮214分别位于第二双向丝杠217的左螺旋段和右螺旋段上,第四电机218驱动所述第二双向丝杠217转动以改变所述主动摩擦轮213和所述从动摩擦轮214之间的距离,以便于不同尺寸轴瓦10的安放。
如图4所示,所述焊接模块30具有一矩形钢底座,所述矩形钢底座上设置有一竖直的焊接支架31,所述焊接支架31通过三角固定架固定在所述矩形钢底座上,所述焊接支架31的一侧安装有两个同步带导轨34,上层同步带导轨34的前端固定有一把焊枪35,而其后端则固定输送焊丝的送丝机34。下层同步带导轨34前端固定有毛刷37,焊接支架31一侧设置有一第一丝杠33,所述焊接支架31顶部设置有第二电机32,以带动第一丝杠33的旋转,两个同步带导轨均安装在第一丝杠33上,通过第一丝杠33转动调节两个所述同步带导轨34在竖直方向上的位置,达到调整焊枪35和毛刷37工作位置的目的。每个所述同步带导轨34均具有自配的伺服电机来实现其前伸和后缩的动作。焊接完成后,毛刷37会对焊接位置刷洗,并且所述毛刷37表面装有粗糙度仪传感器,对轴瓦10内表面进行粗糙度检测,若检测合格,停止焊接、刷洗,进行下一步操作;若检测不合格,焊枪35自动补焊,再刷洗。
进一步,如图5所示,所述卡盘夹紧模块40包括螺旋升降机41及液压三爪卡盘42,所述螺旋升降机41具有两个,两个所述螺旋升降机41用于驱动所述液压三爪卡盘42沿竖直方向运动,以调节所述液压三爪卡盘42的工作位置,整个所述卡盘夹紧模块40机架部分的框架用选定尺寸的方钢管焊接成设计所需的形状,焊接钢管的最大高度由所需要的螺旋升降机41的工作行程调定,在关键承重的地方,焊接加强筋进而加固,整体的框架用螺栓通过底部钢管的螺栓孔定位固定。
可选的,所述液压三爪卡盘42的卡爪部分呈阶梯型,分段加工,有利于轴瓦10的夹持,有利于轴瓦10的夹持,在卡爪内表面压合一种高强度合金层,有效防止磨损,提高效率。
进一步,所述卡爪与所述轴瓦10接触的部分上可以设置一压力传感器,用于探测所述液压三爪卡的夹持力,一方面可以防止夹持力不足,导致轴瓦10脱落,一方面防止夹持力过大,损坏轴瓦10。
如图1和图2所示,所述支撑模块50为整个所述轴瓦10自动焊接装置提供支撑,且所述支撑模块50的表面设置有两个第二导轨51及位于两个所述第二导轨51之间的第二丝杠52和第一双向丝杠54,两个所述导轨槽212的底部与所述第一双向丝杠54螺纹连接,且两个所述导轨槽212分别位于第一双向丝杠54的左螺旋段和右螺旋段上,所述焊接支架31的底部与所述第二丝杠52螺纹连接,两个所述导轨槽212的两端及所述焊接支架31的两端分别设置于两个所述第二导轨51上,所述第二丝杠52和第一双向丝杠54上各连接有一个第三电机53,对应的所述第三电机53分别用于驱动所述第二丝杠52和第一双向丝杠54转动,以改变两个所述轴瓦支座单元21之间的间距及所述焊接模块30在所述支撑模块50上的横向位置。
基于此,如图1-6所示,本实施例根据轴瓦10的直径尺寸范围,提供了两种利用所述轴瓦10自动焊接装置进行轴瓦10自动焊接的方法,第一种方法的步骤包括:
步骤S1:当轴瓦10的直径尺寸d范围为200mm≤d≤400mm时,根据轴瓦10的尺寸调整主动摩擦轮213和从动摩擦轮214之间的间距、两个轴瓦支座单元21之间的间距,并将所述轴瓦10放置在两个轴瓦支座单元21上;
步骤S2:启动第一电机211,所述主动摩擦轮213带动所述轴瓦10旋转;
步骤S3:焊枪35对所述轴瓦10的内表面进行焊接,焊接后粗糙度仪传感器对轴瓦10内壁焊接位置进行粗糙度检测,若检测不合格,焊枪35自动补焊,直至检测合格为止;
步骤S4:毛刷37对焊接部位进行刷洗;
重复执行步骤S3和步骤S4,直至所述轴瓦10焊接完毕。
第二种方法的步骤包括:
步骤S1’:当轴瓦10的直径尺寸d大于400mm时,启动螺旋升降机41,根据所述轴瓦10的尺寸调整液压三爪卡盘42的工作位置;
步骤S2’:用液压三爪卡盘42夹紧轴瓦10内壁,并带动所述轴瓦10旋转;
步骤S3’:焊枪35对所述轴瓦10的内表面进行焊接,焊接后粗糙度仪传感器对轴瓦10内壁焊接位置进行粗糙度检测,若检测不合格,焊枪35自动补焊,直至检测合格为止;
步骤S4’:毛刷37对焊接部位进行刷洗;
重复执行步骤S3’和步骤S4’,直至所述轴瓦焊接完毕。
上述仅为本发明的优选实施例而已,并不对本发明起到任何限制作用。任何所属技术领域的技术人员,在不脱离本发明的技术方案的范围内,对本发明揭露的技术方案和技术内容做任何形式的等同替换或修改等变动,均属未脱离本发明的技术方案的内容,仍属于本发明的保护范围之内。