应用案例
您当前的位置:产品应用
一种石墨框装片装置
一种石墨框装片装置
【申请公布号:CN109950186A;申请权利人:湖南红太阳光电科技有限公司;发明设计人:张宇; 张锦熙;】
摘要:
本发明公开了一种石墨框装片装置,包括石墨框定位组件、上料同步带、下料同步带、用于校正硅片与上料同步带的相对位置的校正组件、用于定位上料同步带上成列硅片的定位组件、平移组件以及升降组件,所述上料同步带和所述下料同步带平行布置于所述石墨框定位组件两侧,所述校正组件和所述定位组件沿所述上料同步带的传送方向布置,所述平移组件横跨于所述石墨框定位组件、上料同步带以及下料同步带上方,所述升降组件安装于所述平移组件上,升降组件上沿所述上料同步带的传送方向均匀安装有多个用于装片的吸盘。本发明具有硅片定位准确、装片动作简单、装片效率高等优点。
主权项:
1.一种石墨框装片装置,其特征在于:包括石墨框定位组件(1)、上料同步带(2)、下料同步带(3)、用于校正硅片(4)与上料同步带(2)的相对位置的校正组件(5)、用于定位上料同步带(2)上成列硅片(4)的定位组件(6)、平移组件(7)以及升降组件(8),所述上料同步带(2)和所述下料同步带(3)平行布置于所述石墨框定位组件(1)两侧,所述校正组件(5)和所述定位组件(6)沿所述上料同步带(2)的传送方向布置,所述平移组件(7)横跨于所述石墨框定位组件(1)、上料同步带(2)以及下料同步带(3)上方,所述升降组件(8)安装于所述平移组件(7)上,升降组件(8)上沿所述上料同步带(2)的传送方向均匀安装有多个用于装片的吸盘(81)。
要求:
1.一种石墨框装片装置,其特征在于:包括石墨框定位组件(1)、上料同步带(2)、下料同步带(3)、用于校正硅片(4)与上料同步带(2)的相对位置的校正组件(5)、用于定位上料同步带(2)上成列硅片(4)的定位组件(6)、平移组件(7)以及升降组件(8),所述上料同步带(2)和所述下料同步带(3)平行布置于所述石墨框定位组件(1)两侧,所述校正组件(5)和所述定位组件(6)沿所述上料同步带(2)的传送方向布置,所述平移组件(7)横跨于所述石墨框定位组件(1)、上料同步带(2)以及下料同步带(3)上方,所述升降组件(8)安装于所述平移组件(7)上,升降组件(8)上沿所述上料同步带(2)的传送方向均匀安装有多个用于装片的吸盘(81)。
2.根据权利要求1所述的石墨框装片装置,其特征在于:所述校正组件(5)包括两个导向排(51)、用于驱动两个导向排(51)相向运动的校正驱动件(52)、以及校正顶升件(53),两个所述导向排(51)对称布置于所述上料同步带(2)两侧,所述校正顶升件(53)位于所述上料同步带(2)下方。
3.根据权利要求1或2所述的石墨框装片装置,其特征在于:所述定位组件(6)包括定位顶升件(61)、定位安装座(62)、两个定位杆(63)、以及用于驱动两个定位杆(63)相向运动的定位驱动件(64),所述定位安装座(62)设于所述定位顶升件(61)上,所述定位驱动件(64)安装于所述定位安装座(62)上并与所述定位杆(63)相连,两个所述定位杆(63)对称布置于所述上料同步带(2)两侧,所述定位杆(63)上沿上料同步带(2)的传送方向均匀安装有多个定位块(67),所述定位块(67)上设有与硅片(4)直角处配合的定位槽(671)。
4.根据权利要求3所述的石墨框装片装置,其特征在于:所述定位槽(671)的侧壁均为斜面。
5.根据权利要求3所述的石墨框装片装置,其特征在于:所述定位安装座(62)上还设有一对定位滑轨(65),所述定位驱动件(64)位于一对所述定位滑轨(65)之间,所述定位杆(63)通过定位滑块(66)滑设于所述定位滑轨(65)上。
6.根据权利要求1所述的石墨框装片装置,其特征在于:所述平移组件(7)包括横跨于所述石墨框定位组件(1)上的平移驱动带(71)以及与平移驱动带(71)固定连接的升降组件安装座(72),所述升降组件(8)安装于所述升降组件安装座(72)上。
7.根据权利要求6所述的石墨框装片装置,其特征在于:所述升降组件(8)包括与所述升降组件安装座(72)相连的升降连接板(86)、安装于所述升降连接板(86)上的升降驱动件(82)、以及与升降驱动件(82)相连的升降支架(83),所述吸盘(81)安装于所述升降支架(83)上。
8.根据权利要求1所述的石墨框装片装置,其特征在于:所述石墨框定位组件(1)包括两组旋转夹紧气缸(11),两组所述旋转夹紧气缸(11)相对布置于石墨框(9)的两侧。
9.根据权利要求1所述的石墨框装片装置,其特征在于:所述平移组件(7)平行设置有两组,所述升降组件(8)包括装片升降组件(84)和卸片升降组件(85),所述装片升降组件(84)安装于其中一组所述平移组件(7)上并在所述石墨框定位组件(1)与所述上料同步带(2)之间平移,所述卸片升降组件(85)安装于另一组所述平移组件(7)上并在所述石墨框定位组件(1)与所述下料同步带(3)之间平移。
一种石墨框装片装置
技术领域
本发明涉及石墨框上下料设备,尤其涉及一种石墨框装片装置。
背景技术
随着光伏技术的不断进步,光伏电池正朝着高效低成本方向发展,同时电池片生产过程的自动化程度也越来越高。由于PERC电池具有转换效率高、与传统电池工艺兼容性好、量产成本降低等优点,高效PERC电池逐渐成为下一代光伏电池的最佳选择。PERC电池的生产工艺流程包括制绒、扩散、刻蚀、退火、背面钝化、镀膜、激光、丝印、烧结和分选,其中背面钝化是最为关键的一道工艺,目前背面钝化工艺普遍采用的工艺设备为背钝化平板PECVD,该设备是目前行业内公认可行的、能够满足光伏产业化需求的Al2O3成膜工艺装备,具有产能高、自动化程度高、成膜均匀、无绕镀、碎片率低等优点。石墨框上下料设备是背钝化平板PECVD的配套设备,用于实现主工艺设备的自动上料和下料。
现有的石墨框上下料设备装片结构不合理,硅片定位不准,装片动作复杂,装片效率低,碎片率高,不能满足主工艺设备日益增长的产能需求,造成严重的产能浪费,严重制约着厂线的生产节拍和生产效率。
发明内容
本发明要解决的技术问题是克服现有技术的不足,提供一种硅片定位准确、装片动作简单、装片效率高的石墨框装片装置。
为解决上述技术问题,本发明采用以下技术方案:
一种石墨框装片装置,包括石墨框定位组件、上料同步带、下料同步带、用于校正硅片与上料同步带的相对位置的校正组件、用于定位上料同步带上成列硅片的定位组件、平移组件以及升降组件,所述上料同步带和所述下料同步带平行布置于所述石墨框定位组件两侧,所述校正组件和所述定位组件沿所述上料同步带的传送方向布置,所述平移组件横跨于所述石墨框定位组件、上料同步带以及下料同步带上方,所述升降组件安装于所述平移组件上,升降组件上沿所述上料同步带的传送方向均匀安装有多个用于装片的吸盘。
作为上述技术方案的进一步改进:
所述校正组件包括两个导向排、用于驱动两个导向排相向运动的校正驱动件、以及校正顶升件,两个所述导向排对称布置于所述上料同步带两侧,所述校正顶升件位于所述上料同步带下方。
所述定位组件包括定位顶升件、定位安装座、两个定位杆、以及用于驱动两个定位杆相向运动的定位驱动件,所述定位安装座设于所述定位顶升件上,所述定位驱动件安装于所述定位安装座上并与所述定位杆相连,两个所述定位杆对称布置于所述上料同步带两侧,所述定位杆上沿上料同步带的传送方向均匀安装有多个定位块,所述定位块上设有与硅片直角处配合的定位槽。
所述定位槽的侧壁均为斜面。
所述定位安装座上还设有一对定位滑轨,所述定位驱动件位于一对所述定位滑轨之间,所述定位杆通过定位滑块滑设于所述定位滑轨上。
所述平移组件包括横跨于所述石墨框定位组件上的平移驱动带以及与平移驱动带固定连接的升降组件安装座,所述升降组件安装于所述升降组件安装座上。
所述升降组件包括与所述升降组件安装座相连的升降连接板、安装于所述升降连接板上的升降驱动件、以及与升降驱动件相连的升降支架,所述吸盘安装于所述升降支架上。
所述石墨框定位组件包括两组旋转夹紧气缸,两组所述旋转夹紧气缸相对布置于石墨框的两侧。
所述平移组件平行设置有两组,所述升降组件包括装片升降组件和卸片升降组件,所述装片升降组件安装于其中一组所述平移组件上并在所述石墨框定位组件与所述上料同步带之间平移,所述卸片升降组件安装于另一组所述平移组件上并在所述石墨框定位组件与所述下料同步带之间平移。
与现有技术相比,本发明的优点在于:本发明公开的石墨框装片装置,将上料同步带和下料同步带平行布置在石墨框定位组件两侧,平移组件横跨于上料同步带和下料同步带之上,利用平移组件带动升降组件在上料同步带、石墨框定位组件、下料同步带之间来回移动,升降组件上安装吸盘,通过吸盘实现装、卸片,各部件布局合理,简化了装片动作,提高了装片效率;利用校正组件校正硅片的位置,使硅片与上料同步带相对位置准确,硅片传送到位后利用定位组件对上料同步带上成列的硅片进行定位,确保各硅片之间的相对位置准确,保证装片时所有硅片分别被各吸盘准确地吸取,避免了碎片。
附图说明
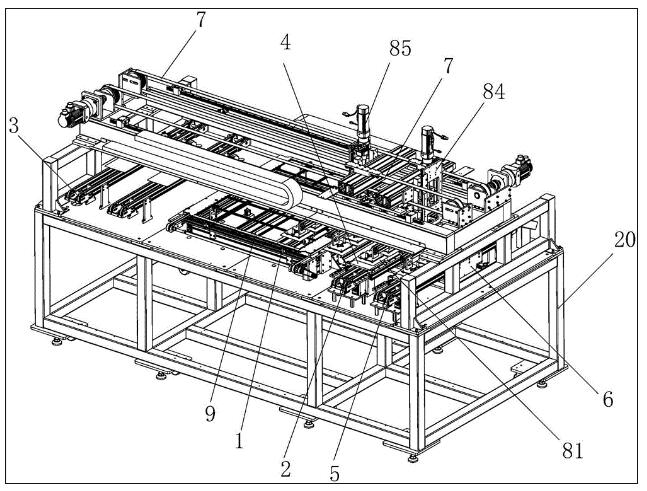
图1是本发明石墨框装片装置的立体结构示意图。
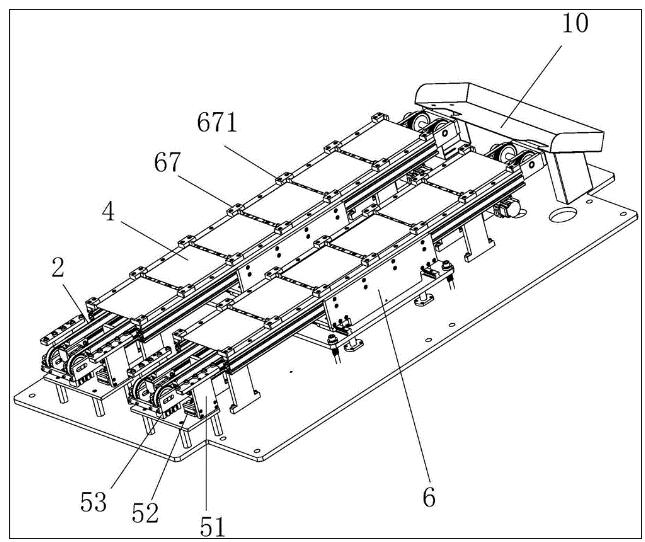
图2是是本发明中的上料同步带、校正组件和定位组件的立体结构示意图。
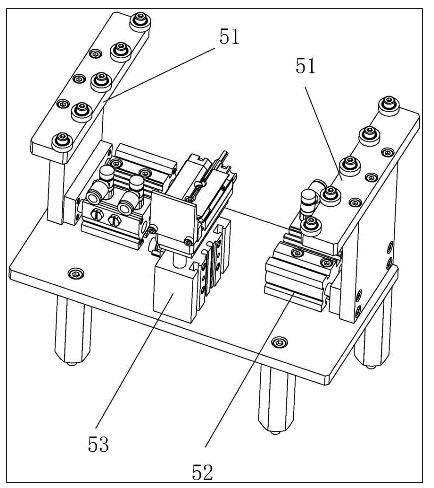
图3是本发明中的校正组件的立体结构示意图。
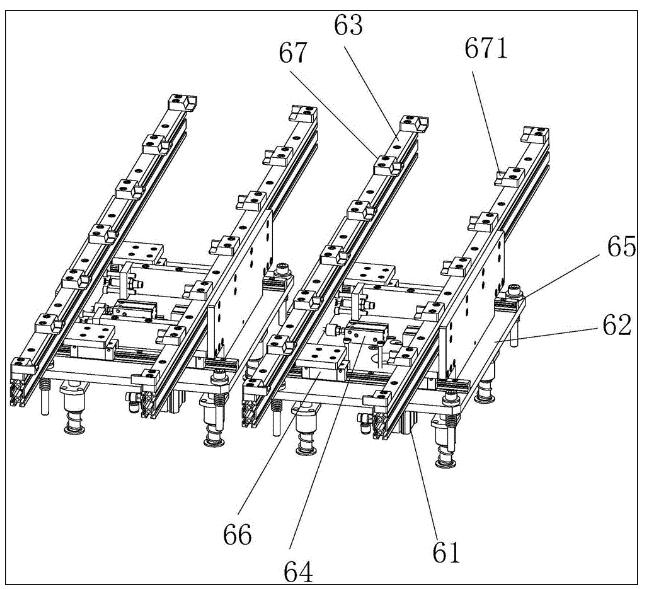
图4是本发明中的定位组件的立体结构示意图。
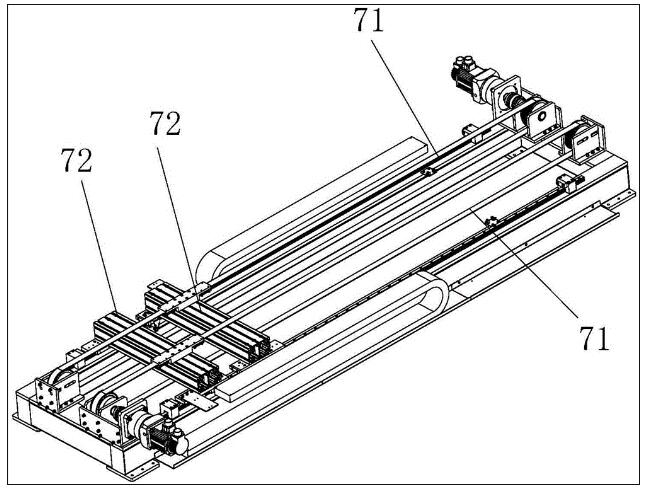
图5是本发明中的平移组件的立体结构示意图。
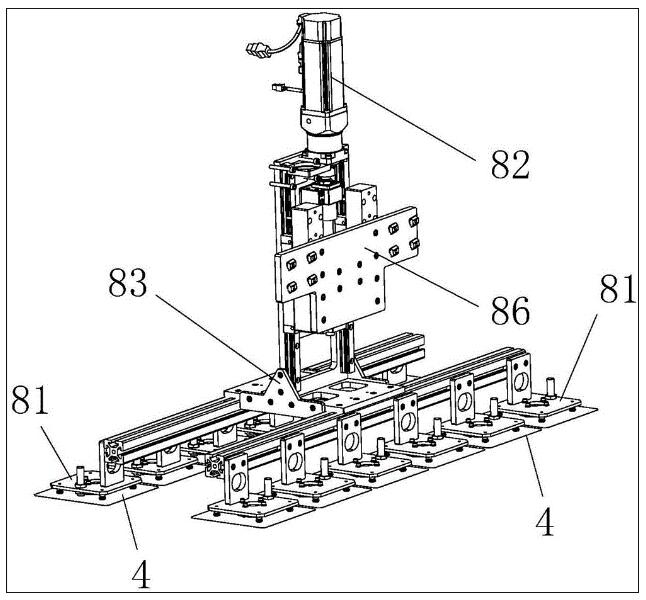
图6是本发明中的升降组件的立体结构示意图。
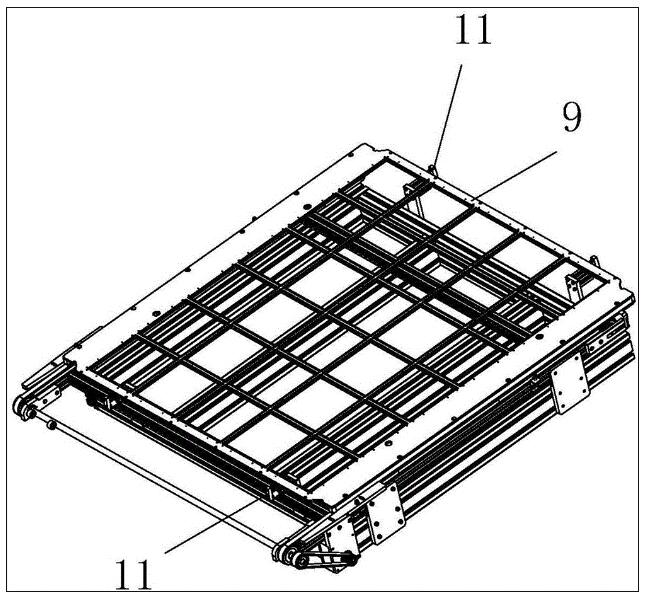
图7是本发明中的石墨框定位组件的立体结构示意图。
图中各标号表示:1、石墨框定位组件;11、旋转夹紧气缸;2、上料同步带;3、下料同步带;4、硅片;5、校正组件;51、导向排;52、校正驱动件;53、校正顶升件;6、定位组件;61、定位顶升件;62、定位安装座;63、定位杆;64、定位驱动件;65、定位滑轨;66、定位滑块;67、定位块;671、定位槽;7、平移组件;71、平移驱动带;72、升降组件安装座;8、升降组件;81、吸盘;82、升降驱动件;83、升降支架;84、装片升降组件;85、卸片升降组件;86、升降连接板;9、石墨框;10、废片收集盒;20、机架。
具体实施方式
以下结合说明书附图和具体实施例对本发明作进一步详细说明。
图1至图7示出了本发明的一种实施例,本实施例的石墨框装片装置,包括石墨框定位组件1、上料同步带2、下料同步带3、用于校正单片硅片4与上料同步带2的相对位置的校正组件5、用于定位上料同步带2上成列硅片4的定位组件6、平移组件7以及升降组件8,上料同步带2和下料同步带3平行布置于石墨框定位组件1两侧,校正组件5和定位组件6沿上料同步带2的传送方向布置,平移组件7横跨于石墨框定位组件1、上料同步带2以及下料同步带3上方,升降组件8安装于平移组件7上,升降组件8上沿上料同步带2的传送方向均匀安装有多个用于装片的吸盘81。
该石墨框装片装置,其上料同步带2和下料同步带3平行布置在石墨框定位组件1两侧,平移组件7横跨于上料同步带2和下料同步带3之上,利用平移组件7带动升降组件8在上料同步带2、石墨框定位组件1、下料同步带3之间来回移动,升降组件8上安装吸盘81,通过吸盘81实现装、卸片,各组件布局合理,简化了装片动作,提高了装片效率;利用校正组件5校正硅片4与上料同步带2的相对位置,硅片4传送到位后利用定位组件6对上料同步带2上成列的硅片4进行定位,确保各硅片4之间的相对位置准确,保证装片时所有硅片4分别被各吸盘81准确地吸取,避免了碎片。
进一步地,校正组件5包括两个导向排51、用于驱动两个导向排51相向运动的校正驱动件52、以及校正顶升件53,两个导向排51对称布置于上料同步带2两侧,校正顶升件53位于上料同步带2下方。本实施例中,校正驱动件52为两个布置方向相反的气缸,利用气缸活塞杆的伸缩带动导向排51移动;校正顶升件53同样采用气缸,当然在其他实施例中各驱动件也可采用已知的部件、设备实现功能。上游流转下来的硅片4运动至校正组件5时,两个导向排51向中间靠拢,对硅片4进行横向(或称左右方向)定位、导向,校正顶升件53向上方伸出,用于硅片4前后方向的定位,硅片4各方向的偏移被有效限制,硅片4的中心线(硅片4的中心线有两条,此处为沿着上料同步带2传送方向的那条)与上料同步带2的中心线重合,高度适当,从而准确地传输至上料同步带2上,为后续精准的定位、装片等做好准备。
更进一步地,定位组件6包括定位顶升件61、定位安装座62、两个定位杆63、以及用于驱动两个定位杆63相向运动的定位驱动件64,定位安装座62设于定位顶升件61上,定位驱动件64安装于定位安装座62上并与定位杆63相连,两个定位杆63对称布置于上料同步带2两侧,定位杆63上沿上料同步带2的传送方向均匀安装有多个定位块67,定位块67上设有与硅片4直角处配合的定位槽671。本实施例中,定位顶升件61为气缸,定位驱动件64为两个布置方向相反的气缸,当然在其他实施例中各驱动件也可采用已知的部件、设备实现功能。上料同步带2在伺服电机、同步带轮的驱动下按照设定的距离等距离地将硅片4前传送,摆成一列,定位顶升件61通过定位安装座62驱动两个定位杆63上升,定位驱动件64驱动两个定位杆63向中间靠拢,硅片4的四角分别进入不同的定位槽671内,从而对成列的硅片4进行二次横向导正,保证装片前各硅片4精确定位。
更进一步地,本实施例中,定位槽671的侧壁均为斜面。硅片4进入定位槽671之后,在重力作用下向下滑动至定位槽671的底部,有利于保证定位精确,结构简单、可靠。
更进一步地,本实施例中,定位安装座62上还设有一对定位滑轨65,定位驱动件64位于一对定位滑轨65之间,定位杆63通过定位滑块66滑设于定位滑轨65上。通过定位滑轨65与定位滑块66的配合,避免定位杆63位置出现偏差,同时使定位杆63移动过程更平稳、顺畅。
进一步地,平移组件7包括横跨于石墨框定位组件1上的平移驱动带71以及与平移驱动带71固定连接的升降组件安装座72,升降组件8安装于升降组件安装座72上。其中,平移驱动带71由伺服电机、同步带轮驱动实现运转,带动升降组件安装座72来回平移,进而带动升降组件8实现平移,结构简单、可靠。升降组件安装座72优选采用型材制作,位于平移驱动带71上下两部分之间,使结构更紧凑。
进一步地,升降组件8包括与升降组件安装座72相连的升降连接板86、安装于升降连接板86上的升降驱动件82、以及与升降驱动件82相连的升降支架83,吸盘81安装于升降支架83上。本实施例中,升降驱动件82为丝杠螺母机构,通过伺服电机驱动丝杠旋转,带动升降支架83上下移动。需要装片时,升降支架83带动各吸盘81下降吸住下方对应的硅片4即可。
进一步地,石墨框定位组件1包括两组旋转夹紧气缸11,两组旋转夹紧气缸11相对布置于石墨框9的两侧。石墨框9传送到位后,两组旋转夹紧气缸11旋转并从石墨框9两侧夹紧,保证石墨框9定位可靠。其中各组旋转夹紧气缸11采用两个旋转夹紧气缸11。
进一步地,本实施例中,平移组件7平行设置有两组,升降组件8包括装片升降组件84和卸片升降组件85,装片升降组件84安装于其中一组平移组件7上并在石墨框定位组件1与上料同步带2之间平移,卸片升降组件85安装于另一组平移组件7上并在石墨框定位组件1与下料同步带3之间平移。平移组件7设置两组,升降组件8也设置为两组,装片升降组件84由其中一组平移组件7带动在上料同步带2和石墨框9之间平移用于装片,卸片升降组件85由另一组平移组件7带动在下料同步带3和石墨框9之间平移用于卸片,使得装片和卸片可同时进行,互不干扰,大大提升了装卸硅片4的效率。优选地,上料同步带2、下料同步带3也设置为两列,装片升降组件84和卸片升降组件85也均安装两列吸盘81。
本发明石墨框装片装置的工作过程如下:
石墨框9运动到位后,被石墨框定位组件1固定,上游流转下来的硅片4运动至校正组件5进行校正,然后顺利传送至上料同步带2上,上料同步带2在伺服电机、同步带轮的驱动下按照设定的距离等距离地将硅片4前传送,摆成一列,碎片、不良硅片4被末端的废片收集盒10收集,定位组件6对成列的硅片4进行二次横向导正,保证定位精确,再然后装片升降组件84下降,其上的吸盘81抓取成列的硅片4,完成抓取之后再上升,与装片升降组件84相连的平移组件7带动装片升降组件84向石墨框9平移,移动到位后,装片升降组件84再次下降将抓取的硅片4放置于石墨框9上,完成装片过程。于此同时,可进行卸片过程:卸片升降组件85下降,其上的吸盘81抓取石墨框9内的硅片4,完成抓取之后再上升,然后与卸片升降组件85相连的平移组件7带动卸片升降组件85向下料同步带3平移,移动到位后,卸片升降组件85再次下降将抓取的硅片4放置于下料同步带3上,下料同步带3将硅片4网下游传送。
虽然本发明已以较佳实施例揭露如上,然而并非用以限定本发明。任何熟悉本领域的技术人员,在不脱离本发明技术方案范围的情况下,都可利用上述揭示的技术内容对本发明技术方案做出许多可能的变动和修饰,或修改为等同变化的等效实施例。因此,凡是未脱离本发明技术方案的内容,依据本发明技术实质对以上实施例所做的任何简单修改、等同变化及修饰,均应落在本发明技术方案保护的范围内。
【申请公布号:CN109950186A;申请权利人:湖南红太阳光电科技有限公司;发明设计人:张宇; 张锦熙;】
摘要:
本发明公开了一种石墨框装片装置,包括石墨框定位组件、上料同步带、下料同步带、用于校正硅片与上料同步带的相对位置的校正组件、用于定位上料同步带上成列硅片的定位组件、平移组件以及升降组件,所述上料同步带和所述下料同步带平行布置于所述石墨框定位组件两侧,所述校正组件和所述定位组件沿所述上料同步带的传送方向布置,所述平移组件横跨于所述石墨框定位组件、上料同步带以及下料同步带上方,所述升降组件安装于所述平移组件上,升降组件上沿所述上料同步带的传送方向均匀安装有多个用于装片的吸盘。本发明具有硅片定位准确、装片动作简单、装片效率高等优点。
主权项:
1.一种石墨框装片装置,其特征在于:包括石墨框定位组件(1)、上料同步带(2)、下料同步带(3)、用于校正硅片(4)与上料同步带(2)的相对位置的校正组件(5)、用于定位上料同步带(2)上成列硅片(4)的定位组件(6)、平移组件(7)以及升降组件(8),所述上料同步带(2)和所述下料同步带(3)平行布置于所述石墨框定位组件(1)两侧,所述校正组件(5)和所述定位组件(6)沿所述上料同步带(2)的传送方向布置,所述平移组件(7)横跨于所述石墨框定位组件(1)、上料同步带(2)以及下料同步带(3)上方,所述升降组件(8)安装于所述平移组件(7)上,升降组件(8)上沿所述上料同步带(2)的传送方向均匀安装有多个用于装片的吸盘(81)。
要求:
1.一种石墨框装片装置,其特征在于:包括石墨框定位组件(1)、上料同步带(2)、下料同步带(3)、用于校正硅片(4)与上料同步带(2)的相对位置的校正组件(5)、用于定位上料同步带(2)上成列硅片(4)的定位组件(6)、平移组件(7)以及升降组件(8),所述上料同步带(2)和所述下料同步带(3)平行布置于所述石墨框定位组件(1)两侧,所述校正组件(5)和所述定位组件(6)沿所述上料同步带(2)的传送方向布置,所述平移组件(7)横跨于所述石墨框定位组件(1)、上料同步带(2)以及下料同步带(3)上方,所述升降组件(8)安装于所述平移组件(7)上,升降组件(8)上沿所述上料同步带(2)的传送方向均匀安装有多个用于装片的吸盘(81)。
2.根据权利要求1所述的石墨框装片装置,其特征在于:所述校正组件(5)包括两个导向排(51)、用于驱动两个导向排(51)相向运动的校正驱动件(52)、以及校正顶升件(53),两个所述导向排(51)对称布置于所述上料同步带(2)两侧,所述校正顶升件(53)位于所述上料同步带(2)下方。
3.根据权利要求1或2所述的石墨框装片装置,其特征在于:所述定位组件(6)包括定位顶升件(61)、定位安装座(62)、两个定位杆(63)、以及用于驱动两个定位杆(63)相向运动的定位驱动件(64),所述定位安装座(62)设于所述定位顶升件(61)上,所述定位驱动件(64)安装于所述定位安装座(62)上并与所述定位杆(63)相连,两个所述定位杆(63)对称布置于所述上料同步带(2)两侧,所述定位杆(63)上沿上料同步带(2)的传送方向均匀安装有多个定位块(67),所述定位块(67)上设有与硅片(4)直角处配合的定位槽(671)。
4.根据权利要求3所述的石墨框装片装置,其特征在于:所述定位槽(671)的侧壁均为斜面。
5.根据权利要求3所述的石墨框装片装置,其特征在于:所述定位安装座(62)上还设有一对定位滑轨(65),所述定位驱动件(64)位于一对所述定位滑轨(65)之间,所述定位杆(63)通过定位滑块(66)滑设于所述定位滑轨(65)上。
6.根据权利要求1所述的石墨框装片装置,其特征在于:所述平移组件(7)包括横跨于所述石墨框定位组件(1)上的平移驱动带(71)以及与平移驱动带(71)固定连接的升降组件安装座(72),所述升降组件(8)安装于所述升降组件安装座(72)上。
7.根据权利要求6所述的石墨框装片装置,其特征在于:所述升降组件(8)包括与所述升降组件安装座(72)相连的升降连接板(86)、安装于所述升降连接板(86)上的升降驱动件(82)、以及与升降驱动件(82)相连的升降支架(83),所述吸盘(81)安装于所述升降支架(83)上。
8.根据权利要求1所述的石墨框装片装置,其特征在于:所述石墨框定位组件(1)包括两组旋转夹紧气缸(11),两组所述旋转夹紧气缸(11)相对布置于石墨框(9)的两侧。
9.根据权利要求1所述的石墨框装片装置,其特征在于:所述平移组件(7)平行设置有两组,所述升降组件(8)包括装片升降组件(84)和卸片升降组件(85),所述装片升降组件(84)安装于其中一组所述平移组件(7)上并在所述石墨框定位组件(1)与所述上料同步带(2)之间平移,所述卸片升降组件(85)安装于另一组所述平移组件(7)上并在所述石墨框定位组件(1)与所述下料同步带(3)之间平移。
一种石墨框装片装置
技术领域
本发明涉及石墨框上下料设备,尤其涉及一种石墨框装片装置。
背景技术
随着光伏技术的不断进步,光伏电池正朝着高效低成本方向发展,同时电池片生产过程的自动化程度也越来越高。由于PERC电池具有转换效率高、与传统电池工艺兼容性好、量产成本降低等优点,高效PERC电池逐渐成为下一代光伏电池的最佳选择。PERC电池的生产工艺流程包括制绒、扩散、刻蚀、退火、背面钝化、镀膜、激光、丝印、烧结和分选,其中背面钝化是最为关键的一道工艺,目前背面钝化工艺普遍采用的工艺设备为背钝化平板PECVD,该设备是目前行业内公认可行的、能够满足光伏产业化需求的Al2O3成膜工艺装备,具有产能高、自动化程度高、成膜均匀、无绕镀、碎片率低等优点。石墨框上下料设备是背钝化平板PECVD的配套设备,用于实现主工艺设备的自动上料和下料。
现有的石墨框上下料设备装片结构不合理,硅片定位不准,装片动作复杂,装片效率低,碎片率高,不能满足主工艺设备日益增长的产能需求,造成严重的产能浪费,严重制约着厂线的生产节拍和生产效率。
发明内容
本发明要解决的技术问题是克服现有技术的不足,提供一种硅片定位准确、装片动作简单、装片效率高的石墨框装片装置。
为解决上述技术问题,本发明采用以下技术方案:
一种石墨框装片装置,包括石墨框定位组件、上料同步带、下料同步带、用于校正硅片与上料同步带的相对位置的校正组件、用于定位上料同步带上成列硅片的定位组件、平移组件以及升降组件,所述上料同步带和所述下料同步带平行布置于所述石墨框定位组件两侧,所述校正组件和所述定位组件沿所述上料同步带的传送方向布置,所述平移组件横跨于所述石墨框定位组件、上料同步带以及下料同步带上方,所述升降组件安装于所述平移组件上,升降组件上沿所述上料同步带的传送方向均匀安装有多个用于装片的吸盘。
作为上述技术方案的进一步改进:
所述校正组件包括两个导向排、用于驱动两个导向排相向运动的校正驱动件、以及校正顶升件,两个所述导向排对称布置于所述上料同步带两侧,所述校正顶升件位于所述上料同步带下方。
所述定位组件包括定位顶升件、定位安装座、两个定位杆、以及用于驱动两个定位杆相向运动的定位驱动件,所述定位安装座设于所述定位顶升件上,所述定位驱动件安装于所述定位安装座上并与所述定位杆相连,两个所述定位杆对称布置于所述上料同步带两侧,所述定位杆上沿上料同步带的传送方向均匀安装有多个定位块,所述定位块上设有与硅片直角处配合的定位槽。
所述定位槽的侧壁均为斜面。
所述定位安装座上还设有一对定位滑轨,所述定位驱动件位于一对所述定位滑轨之间,所述定位杆通过定位滑块滑设于所述定位滑轨上。
所述平移组件包括横跨于所述石墨框定位组件上的平移驱动带以及与平移驱动带固定连接的升降组件安装座,所述升降组件安装于所述升降组件安装座上。
所述升降组件包括与所述升降组件安装座相连的升降连接板、安装于所述升降连接板上的升降驱动件、以及与升降驱动件相连的升降支架,所述吸盘安装于所述升降支架上。
所述石墨框定位组件包括两组旋转夹紧气缸,两组所述旋转夹紧气缸相对布置于石墨框的两侧。
所述平移组件平行设置有两组,所述升降组件包括装片升降组件和卸片升降组件,所述装片升降组件安装于其中一组所述平移组件上并在所述石墨框定位组件与所述上料同步带之间平移,所述卸片升降组件安装于另一组所述平移组件上并在所述石墨框定位组件与所述下料同步带之间平移。
与现有技术相比,本发明的优点在于:本发明公开的石墨框装片装置,将上料同步带和下料同步带平行布置在石墨框定位组件两侧,平移组件横跨于上料同步带和下料同步带之上,利用平移组件带动升降组件在上料同步带、石墨框定位组件、下料同步带之间来回移动,升降组件上安装吸盘,通过吸盘实现装、卸片,各部件布局合理,简化了装片动作,提高了装片效率;利用校正组件校正硅片的位置,使硅片与上料同步带相对位置准确,硅片传送到位后利用定位组件对上料同步带上成列的硅片进行定位,确保各硅片之间的相对位置准确,保证装片时所有硅片分别被各吸盘准确地吸取,避免了碎片。
附图说明
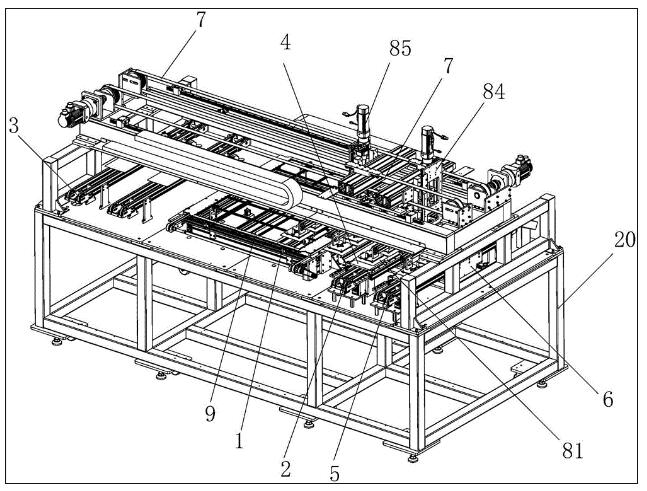
图1是本发明石墨框装片装置的立体结构示意图。
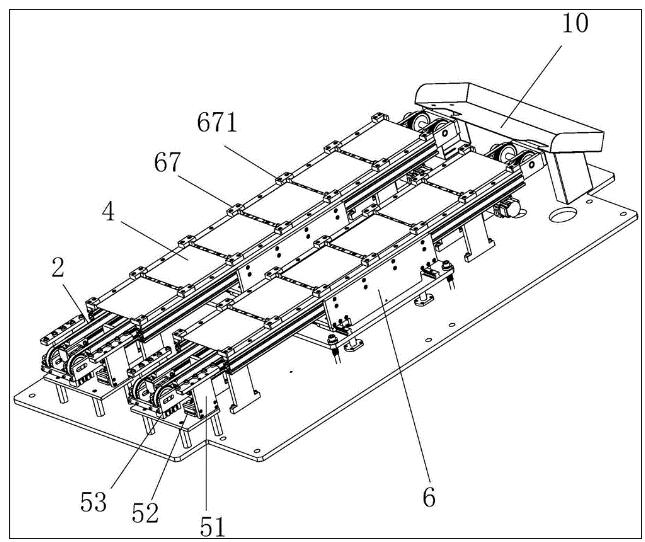
图2是是本发明中的上料同步带、校正组件和定位组件的立体结构示意图。
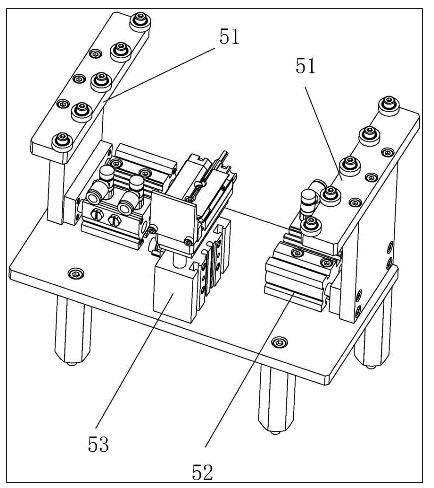
图3是本发明中的校正组件的立体结构示意图。
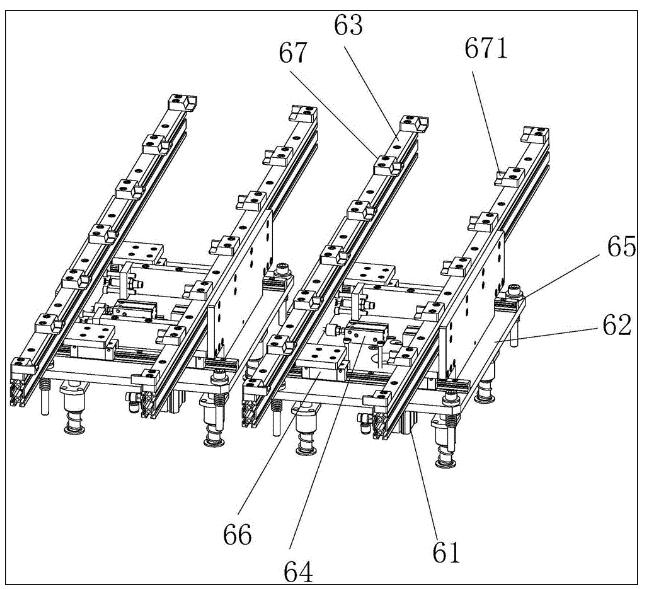
图4是本发明中的定位组件的立体结构示意图。
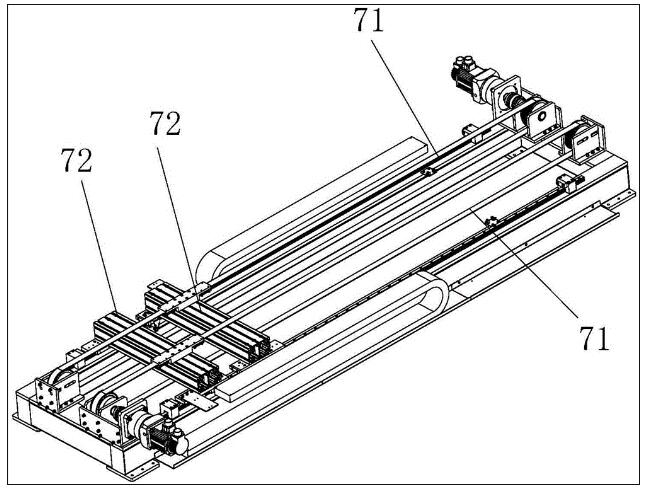
图5是本发明中的平移组件的立体结构示意图。
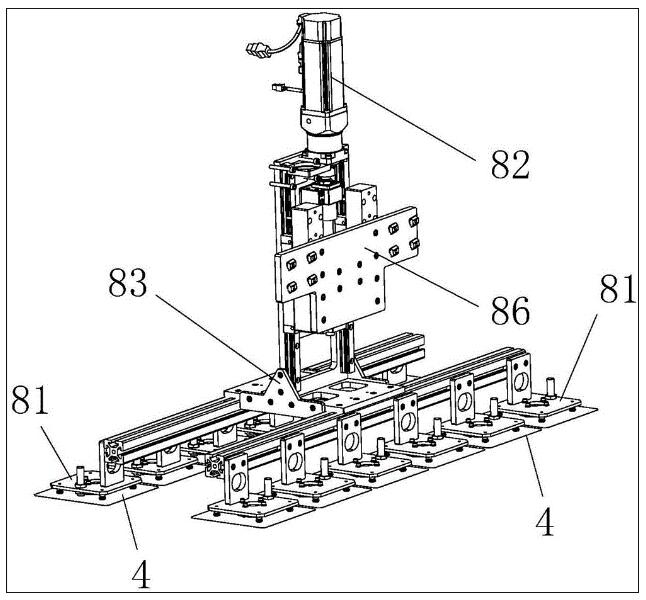
图6是本发明中的升降组件的立体结构示意图。
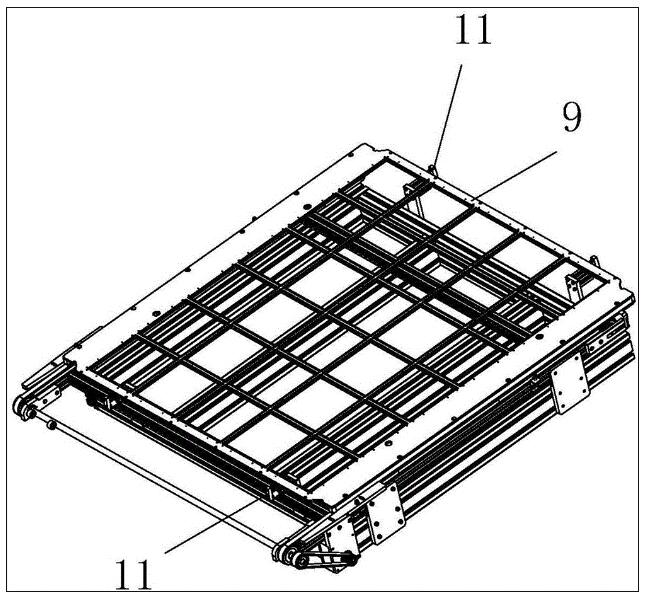
图7是本发明中的石墨框定位组件的立体结构示意图。
图中各标号表示:1、石墨框定位组件;11、旋转夹紧气缸;2、上料同步带;3、下料同步带;4、硅片;5、校正组件;51、导向排;52、校正驱动件;53、校正顶升件;6、定位组件;61、定位顶升件;62、定位安装座;63、定位杆;64、定位驱动件;65、定位滑轨;66、定位滑块;67、定位块;671、定位槽;7、平移组件;71、平移驱动带;72、升降组件安装座;8、升降组件;81、吸盘;82、升降驱动件;83、升降支架;84、装片升降组件;85、卸片升降组件;86、升降连接板;9、石墨框;10、废片收集盒;20、机架。
具体实施方式
以下结合说明书附图和具体实施例对本发明作进一步详细说明。
图1至图7示出了本发明的一种实施例,本实施例的石墨框装片装置,包括石墨框定位组件1、上料同步带2、下料同步带3、用于校正单片硅片4与上料同步带2的相对位置的校正组件5、用于定位上料同步带2上成列硅片4的定位组件6、平移组件7以及升降组件8,上料同步带2和下料同步带3平行布置于石墨框定位组件1两侧,校正组件5和定位组件6沿上料同步带2的传送方向布置,平移组件7横跨于石墨框定位组件1、上料同步带2以及下料同步带3上方,升降组件8安装于平移组件7上,升降组件8上沿上料同步带2的传送方向均匀安装有多个用于装片的吸盘81。
该石墨框装片装置,其上料同步带2和下料同步带3平行布置在石墨框定位组件1两侧,平移组件7横跨于上料同步带2和下料同步带3之上,利用平移组件7带动升降组件8在上料同步带2、石墨框定位组件1、下料同步带3之间来回移动,升降组件8上安装吸盘81,通过吸盘81实现装、卸片,各组件布局合理,简化了装片动作,提高了装片效率;利用校正组件5校正硅片4与上料同步带2的相对位置,硅片4传送到位后利用定位组件6对上料同步带2上成列的硅片4进行定位,确保各硅片4之间的相对位置准确,保证装片时所有硅片4分别被各吸盘81准确地吸取,避免了碎片。
进一步地,校正组件5包括两个导向排51、用于驱动两个导向排51相向运动的校正驱动件52、以及校正顶升件53,两个导向排51对称布置于上料同步带2两侧,校正顶升件53位于上料同步带2下方。本实施例中,校正驱动件52为两个布置方向相反的气缸,利用气缸活塞杆的伸缩带动导向排51移动;校正顶升件53同样采用气缸,当然在其他实施例中各驱动件也可采用已知的部件、设备实现功能。上游流转下来的硅片4运动至校正组件5时,两个导向排51向中间靠拢,对硅片4进行横向(或称左右方向)定位、导向,校正顶升件53向上方伸出,用于硅片4前后方向的定位,硅片4各方向的偏移被有效限制,硅片4的中心线(硅片4的中心线有两条,此处为沿着上料同步带2传送方向的那条)与上料同步带2的中心线重合,高度适当,从而准确地传输至上料同步带2上,为后续精准的定位、装片等做好准备。
更进一步地,定位组件6包括定位顶升件61、定位安装座62、两个定位杆63、以及用于驱动两个定位杆63相向运动的定位驱动件64,定位安装座62设于定位顶升件61上,定位驱动件64安装于定位安装座62上并与定位杆63相连,两个定位杆63对称布置于上料同步带2两侧,定位杆63上沿上料同步带2的传送方向均匀安装有多个定位块67,定位块67上设有与硅片4直角处配合的定位槽671。本实施例中,定位顶升件61为气缸,定位驱动件64为两个布置方向相反的气缸,当然在其他实施例中各驱动件也可采用已知的部件、设备实现功能。上料同步带2在伺服电机、同步带轮的驱动下按照设定的距离等距离地将硅片4前传送,摆成一列,定位顶升件61通过定位安装座62驱动两个定位杆63上升,定位驱动件64驱动两个定位杆63向中间靠拢,硅片4的四角分别进入不同的定位槽671内,从而对成列的硅片4进行二次横向导正,保证装片前各硅片4精确定位。
更进一步地,本实施例中,定位槽671的侧壁均为斜面。硅片4进入定位槽671之后,在重力作用下向下滑动至定位槽671的底部,有利于保证定位精确,结构简单、可靠。
更进一步地,本实施例中,定位安装座62上还设有一对定位滑轨65,定位驱动件64位于一对定位滑轨65之间,定位杆63通过定位滑块66滑设于定位滑轨65上。通过定位滑轨65与定位滑块66的配合,避免定位杆63位置出现偏差,同时使定位杆63移动过程更平稳、顺畅。
进一步地,平移组件7包括横跨于石墨框定位组件1上的平移驱动带71以及与平移驱动带71固定连接的升降组件安装座72,升降组件8安装于升降组件安装座72上。其中,平移驱动带71由伺服电机、同步带轮驱动实现运转,带动升降组件安装座72来回平移,进而带动升降组件8实现平移,结构简单、可靠。升降组件安装座72优选采用型材制作,位于平移驱动带71上下两部分之间,使结构更紧凑。
进一步地,升降组件8包括与升降组件安装座72相连的升降连接板86、安装于升降连接板86上的升降驱动件82、以及与升降驱动件82相连的升降支架83,吸盘81安装于升降支架83上。本实施例中,升降驱动件82为丝杠螺母机构,通过伺服电机驱动丝杠旋转,带动升降支架83上下移动。需要装片时,升降支架83带动各吸盘81下降吸住下方对应的硅片4即可。
进一步地,石墨框定位组件1包括两组旋转夹紧气缸11,两组旋转夹紧气缸11相对布置于石墨框9的两侧。石墨框9传送到位后,两组旋转夹紧气缸11旋转并从石墨框9两侧夹紧,保证石墨框9定位可靠。其中各组旋转夹紧气缸11采用两个旋转夹紧气缸11。
进一步地,本实施例中,平移组件7平行设置有两组,升降组件8包括装片升降组件84和卸片升降组件85,装片升降组件84安装于其中一组平移组件7上并在石墨框定位组件1与上料同步带2之间平移,卸片升降组件85安装于另一组平移组件7上并在石墨框定位组件1与下料同步带3之间平移。平移组件7设置两组,升降组件8也设置为两组,装片升降组件84由其中一组平移组件7带动在上料同步带2和石墨框9之间平移用于装片,卸片升降组件85由另一组平移组件7带动在下料同步带3和石墨框9之间平移用于卸片,使得装片和卸片可同时进行,互不干扰,大大提升了装卸硅片4的效率。优选地,上料同步带2、下料同步带3也设置为两列,装片升降组件84和卸片升降组件85也均安装两列吸盘81。
本发明石墨框装片装置的工作过程如下:
石墨框9运动到位后,被石墨框定位组件1固定,上游流转下来的硅片4运动至校正组件5进行校正,然后顺利传送至上料同步带2上,上料同步带2在伺服电机、同步带轮的驱动下按照设定的距离等距离地将硅片4前传送,摆成一列,碎片、不良硅片4被末端的废片收集盒10收集,定位组件6对成列的硅片4进行二次横向导正,保证定位精确,再然后装片升降组件84下降,其上的吸盘81抓取成列的硅片4,完成抓取之后再上升,与装片升降组件84相连的平移组件7带动装片升降组件84向石墨框9平移,移动到位后,装片升降组件84再次下降将抓取的硅片4放置于石墨框9上,完成装片过程。于此同时,可进行卸片过程:卸片升降组件85下降,其上的吸盘81抓取石墨框9内的硅片4,完成抓取之后再上升,然后与卸片升降组件85相连的平移组件7带动卸片升降组件85向下料同步带3平移,移动到位后,卸片升降组件85再次下降将抓取的硅片4放置于下料同步带3上,下料同步带3将硅片4网下游传送。
虽然本发明已以较佳实施例揭露如上,然而并非用以限定本发明。任何熟悉本领域的技术人员,在不脱离本发明技术方案范围的情况下,都可利用上述揭示的技术内容对本发明技术方案做出许多可能的变动和修饰,或修改为等同变化的等效实施例。因此,凡是未脱离本发明技术方案的内容,依据本发明技术实质对以上实施例所做的任何简单修改、等同变化及修饰,均应落在本发明技术方案保护的范围内。